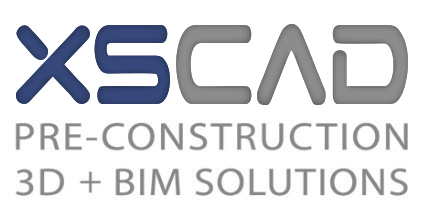
Is BIM creating scope overlap in the M&E industry?
The successful control of BIM models between consultants and contractors in the MEP (M&E) industry continues to be a challenge, and the question of ‘who does what’ has re-emerged now that parametric 3D model-based building services design and coordination processes are becoming more prominent.
Some of the benefits of BIM include: greater relationships among stakeholders, less constructability issues on-site, enhanced design performance and cost efficiency. To apply BIM, scope definition and delivery must be managed effectively, along with the collaboration between MEP (M&E) consultants, contractors, sub-contractors and shop fabricators. Despite its benefits, BIM can create scope overlap between these consultants, contractors and others involved, meaning the project could incur costs and even delays.
Usually, with 2D design data, services coordination and clash detection fall under the responsibility of the MEP contractor. They overlay each of the 2D drawings (for HVAC, electrical and plumbing services) and use either 3D or BIM tools to complete a detailed coordination exercise. A spatially coordinated model is the outcome, which could be used for the creation of installation drawings and later fittings/installations.
This 2D drawing deliverables method means design consultants do not have to focus on constructability and spatial coordination. Nevertheless, the BIM procedure requires clash-free 3D MEP models to be produced by MEP (M&E) BIM consultants before 2D designs drawings for contractors are created.
The consultant effectively carries some of the scope that contractors usually implement when they provide their BIM model (which is increasingly clash free and coordinated to some extent). Despite this, the model is not always coordinated in the way that services would be installed, nor is it cost effective for an MEP contractor.
There is a possibility that the 3D model contributed to the contractor may fall short, even if the consultants’ BIM MEP model is clash-free and spatially coordinated with the architectural and structural systems. The reasons for this are: I) acquisition changes for equipment and materials; ii) the model is unrepresentative of the layout or installation process; iii) inefficient layouts such as allowing for too many bends and connections; iv) inadequate allowance for lagging; v) inadequate allowance for installation/hanging; and vi) no allowance for entry for maintenance purposes. Overall, though spatially coordinated the consultant’s 3D model may be inadequate for installation.
If the BIM model is not revised to the contractor’s individual fitting and installation requirements these issues will only be encountered when in the field. By then, major changes cannot be made and installation will be compromised as reviews and revised/repeated model drawings will increase costs and fees. This is the main area of scope overlap and will affect project profitability and schedules.
This overlap can be seen as defeating the purpose of employing MEP (M&E) BIM methods. The scope can be reduced if more time is reserved to define the deliverables of all parties at the beginning of the process.
Three alternatives are offered to avoid such scope overlap. Firstly, the consultants may not focus on producing a coordinated or clash free model when creating their BIM model. They would then create their design drawings, providing the contractor with a model that has adequate routes and outlets for services, though it is not coordinated. This approach reduces the consultant’s BIM modelling time.
Secondly, a traditional, non-BIM era 2D design could be created. The project’s call for BIM will be served as it still permits the contractor’s to produce a BIM model. This method also means, if required, the contractor can use specialist MEP coordination firms to produce a coordinated BIM model.
The final approach is to employ a specialist MEP coordination firm that possess the required skills, such as knowledge of installation. This means the output could be more useful to contractors who can then perfect the model and create drawings.
Scope overlap in MEP projects can be reduced if one of these approaches is applied. Projects can also be managed and delivered more effectively during the pre-construction and BIM stages. This will be advantageous for clients and a more constructive and efficient use of BIM technology when delivering MEP BIM projects.