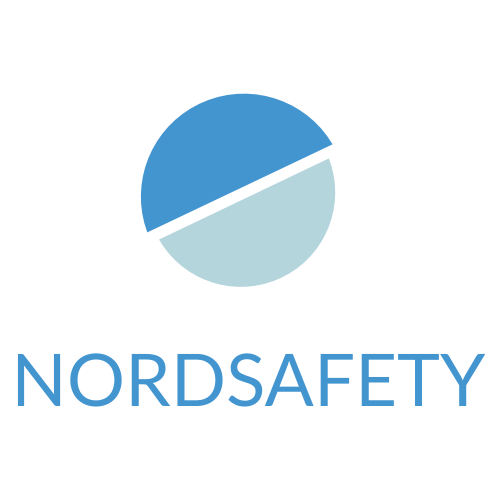
Making safety a habit with improved on-site reporting
Within his blog posts, my fellow founder of NordSafety, Timo Kronlöf, has discussed how safety should be encouraged as an engrained habit, rather than a mandatory chore. And it’s easy to agree from a cultural point of view, that voluntary habits stick better than enforced regulatory processes. We can probably all also agree that creating an outstanding safety culture helps your organisation to operate at its best – to turn this into a reality, I believe that technology can support the implementation of safety as an ongoing habitual practice.
We jointly gave this subject a lot of thought when considering how to engage people more with safety. One particular solution we came up with was to combine safety with work progress reporting functions. These progress and quality reports and documentation stand at the core of the production process, done on daily basis – therefore, it seems natural that safety reporting should also be undertaken at this point, moving the risk identification to a continuous process.
We’ve made this happen by combining our quality and on-site information management features within NordSafety. With one integrated solution, you can handle progress reporting, safety and quality. Whilst this doesn’t completely remove the processes undertaken by Safety Management, engaging your whole workforce with safety, and providing them with the tools that enable them to be the Safety Manager of their own work, is a proven safety model.
The handling of on-site project information is an important factor of HSEQ, requiring items such as progress reports, accurately recorded site diaries, site memos, and start and hand-over inspections. Bringing these features into NordSafety strengthens our strategy for engaging workers with safety, and differentiates our software platform. Solutions that aren’t built as native cloud platforms are not able to support the different reporting needs that are found out in the field every day. Lacking the capability to combine on-site project reporting, safety and quality doesn’t support the safety-as-a-habit improvement. It also doesn’t facilitate the on-site staff to be more productive with increased safety and quality.
As a conclusion, you might say that there is huge potential to digitalise on-site information management by connecting different process together. It increases productivity, and makes it easier to comply with the mandatory reporting needs. Tools which can all be found within the NordSafety application.