News - Construction News
Laying the foundations for the future of housing
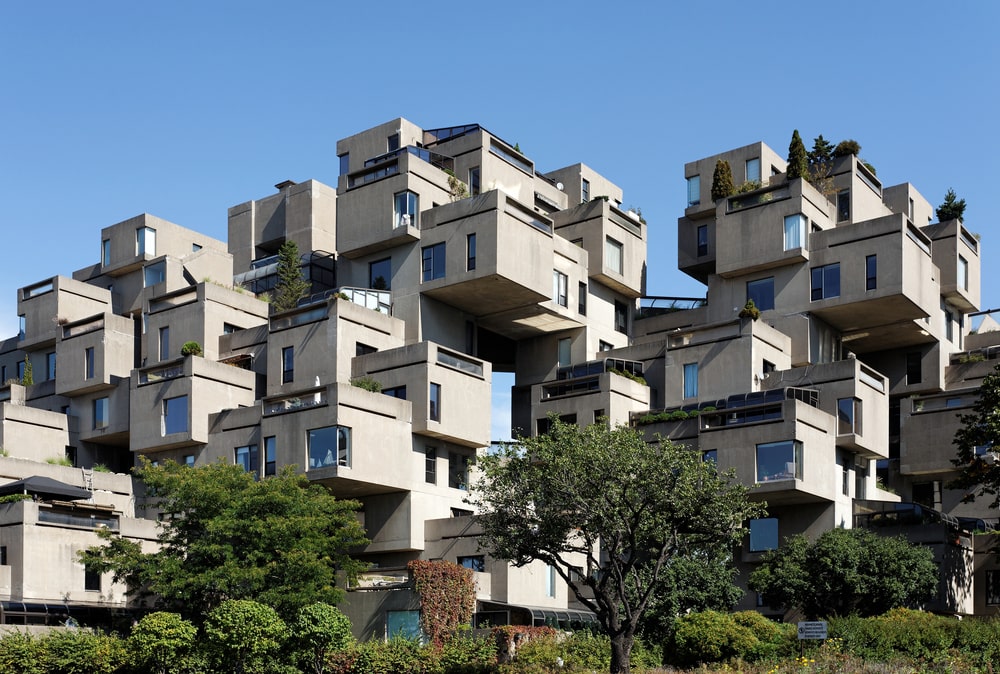
Housing charity Shelter has estimated that the UK will need three million new social homes over the next 20 years to address and solve the nation’s considerable housing shortage, writes Kenny Ingram, Global Industry Director at IFS. Young people and families are being priced out of the housing market, heavy regulations complicate planning applications, and the number of rough sleepers in London rose to a new high in Q4 2018, up 25% over 12 months.
There are, however, a number of other challenges which currently dog innovation in the construction sector and housing development. First, the industry is heavily reliant on migrant labour; non-UK nationals accounted for 40% of the buildings workforce in London, for example. With Brexit on the horizon, the UK could well experience a talent drain, with labourers choosing countries with more attractive (and guaranteed) career opportunities. Construction companies are already struggling to recruit skilled labourers; a situation which could easily worsen.
Second, the sector has been slow to adopt new technologies and approaches. According to one estimate, almost two thirds of those working in the sector believe it is behind others when it comes to adopting digital technology. Slow adoption of new software, innovative materials and digital-first techniques means many companies are still reliant on spreadsheets and manual, outdated methods of data gathering. As a result, they lack visibility into their operations which creates a major stumbling block to managing and monitoring projects, their workforce and their finances. Indeed, the collapse of Carillion last year can in some part be attributed to the fact that the company simply couldn’t see the severity of the situation it had gotten itself into, until it was too late. And it’s not the only one; in the wake of Carillion’s liquidation, the UK saw a reported 20% spike in the number of UK building firms becoming insolvent.
Finally (and linking the above two), a hesitancy to adopt (or lack of knowledge of) new technologies may also have an impact on the make-up of the workforce, compounding the current skills shortage. Why would the digital-first generation of school leavers want to work in an industry whose outlook and IT infrastructure are dated, when they can choose other industries which have embraced digital disruption and invested in R&D and cutting-edge tech?
Building a case for digitalisation
But it’s not all doom and gloom. Despite the slow adoption of new technologies and processes, there is at least a real recognition that doing so is crucial to firms’ success: almost three quarters of construction companies believe that those which do not implement digital ways of working will go out of business. Change is taking place in the industry through the arrival of new players – as well as old faces keen to compete. These names include Amazon, which in 2018 invested in California-based modular house building firm Plant Prefab; and BoKlok (jointly owned by IKEA and construction firm Skanska), which has signed a deal with Worthing Council to deliver affordable factory-built homes.
Rather than being indicators of a growing and diversifying sector however, the arrival of companies such as Amazon will strike fear into many of the traditional operators in the construction industry. Where Amazon leads, others follow – and the same applies here, as the company’s move reflects an emerging trend: modular construction.
This is a 21st century re-imagining of the post-war boom in prefab homes which saw over 150,000 houses spring up between 1946-47. In the 1940’s they provided a solution to rapidly house those who’d lost their homes during the war, and today, modular construction could be the answer to a very similar housing shortage in the UK. The difference ends there though, as new approaches are facilitating the production of cost-efficient, high-quality homes, using the latest technologies and minimising waste material. Building homes in factories also requires less labour and is a far more efficient process, with work unaffected by adverse weather and the logistics problems that impact on-site builds. Finally, project timescales are dramatically reduced and both the delivery of the projects and the resulting constructions are more eco-friendly and safer than traditional builds.
Post-war pre-fab to high-tech fabulous
Change may be gradual – but it is happening. Berkeley Group, for instance, has established Berkeley Modular and has a purpose-built manufacturing facility in Kent; Swan Housing Association/NU BUILD opened an offsite modular factory in Basildon in 2017 and have been delivering high-spec homes since; with while companies like nHouse and Go Modular are creating environmentally-friendly homes in a fraction of the time of traditional builds.
Modular house-building may help tackle the UK’s housing shortage, but the new approaches involved are not without their challenges. Approaches include using virtual reality and 4D planning in the design stage; procurement and manufacturing involving 3D printing; delivering building information modelling (BIM) data on projects; and the use of robotics and drones.
What all these examples have in common – and what is still lacking in much of the sector – is their use of and reliance on, enterprise-wide technology. Modular house-building also demands standardisation of processes and components in a controlled factory environment. This cannot be achieved with the traditional approaches and tools many construction firms still rely on today. Instead, a single centralised software platform is required to provide proper governance and management of projects, and to ensure complete visibility into all components and operations in real time.
An enterprising approach
This will sound daunting to many firms. But the approaches listed above don’t all have to be adopted at once. Introducing enterprise resource planning (ERP) technology that’s suited to the needs of the business and industry will help reduce timeline and budget failures, eliminate non-value-added work, compress timelines and let contractors deliver more value to asset owners with fewer resources.
Whether it’s modular homes or more traditional builds, having an insight into the complete lifecycle of a project is key – and it’s only by investing in new software and technologies that you’ll get that ‘single source of truth.’ And whichever party leader gets the keys to number 10, I hope to see a commitment to delivering affordable housing coupled with investment in new technologies and approaches – in both the public and private sectors.
If you would like to read more articles like this then please click here.
Related Articles
More News
- UK Introduces New Trade Measures to Support Steel Sector
11 Jul 25
Steel producers across the UK will benefit from stronger trade measures from 1 July.
- Clean energy future to be ‘built in Britain’
10 Jul 25
The Clean Energy Industries Sector Plan comes into force to ‘build it in Britain’.
- Thousands more to get the tools they need to start construction careers
9 Jul 25
Thousands of people are set to benefit from on-the-job training and career opportunities in the