News - Construction News
Prioritising full lifecycle assessment
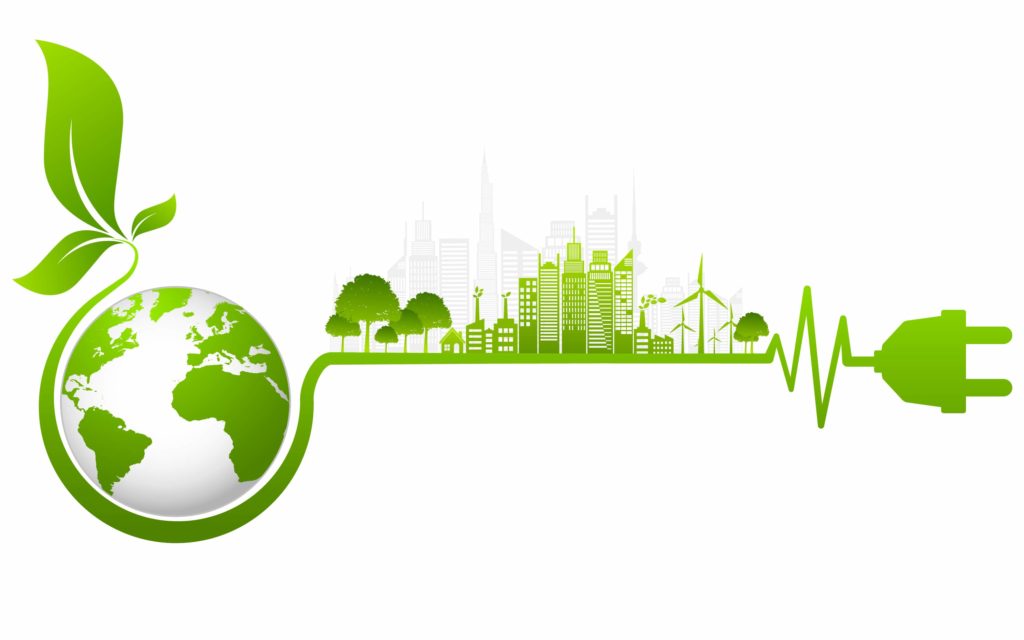
As ambitious pledges and net zero targets emerged from COP26 last year, many industries, not least the built environment, acknowledged the urgent need for decarbonisation – and fast. For the industry to meet climate ambitions, we must prioritise full lifecycle assessment.
The construction sector, responsible for 11% of all carbon emissions worldwide, with embodied carbon from construction making up over 50% of emissions in new projects, has an immense opportunity to make a meaningful difference to offsetting the climate crisis. It’s a goal well worth striving for, but getting there means turning good intentions into solid action now.
In 2022, says Matt Bennion, CEO of Reds10, one of the most important things the industry can do is shift its focus to assessing the full carbon impact of building lifecycles. At the end of last year SCAPE, together with leading industry names, called for an overhaul of procurement in public sector construction to make lifecycle assessments the priority in decision making, and for this to become a statutory obligation. At Reds10 we wholeheartedly support this movement, as it would foster greater accountability and responsible practice.
Government targets and regulations – such as the Construction Playbook’s ‘comply or explain’ basis for sustainable development practices – and initiatives such as SCAPE are doing their bit to provide a framework for transformation. The onus is now on the industry to change how it assesses the true carbon implications of material and design choices and new technologies.
Whole Life Cycle Carbon Assessment (WLCA) can bring full visibility of carbon across the lifecycles of buildings and, if we address the challenges that have previously stood in the way of effective WLCA, it will be a game-changer for accelerating tangible progress.
Overcoming the roadblocks
There are still challenges to collecting clear and relevant information relating to lifecycle performance, with reliable and up-to-date data difficult to find. Traditional construction methods are fragmented and hindered by siloes – existing benchmarks are either not representative of current practices, not backed up by data from real projects, or out of date. WLCA can only help in the case of accurate and good quality data, not only for understanding the carbon footprint of design choices but also for setting future benchmarks. Data that is relevant to proposed developments is often unavailable at the start of projects but it’s the early decisions being made at that stage that ultimately impact the sustainability implications of building lifecycles. At present, these decisions are often based on supposition or guesswork.
It’s also difficult to get accurate data on the sustainability credentials of materials, as in the case of steel, for instance. Steel production has evolved to be more environmentally-friendly through green hydrogen and other green innovations but still often gets discounted based on out of date carbon data. Failing to consider alternative materials can be harmful to delivering on carbon targets, particularly when, like steel, they are infinitely recyclable and can be re-used beyond existing building lifecycles.
MMC to drive sustainability
As well as alternative materials, we must also leave room for alternative methods of construction. The methodology of MMC is ideally suited to tackling the abovementioned hurdles, as it delivers higher quality buildings much more sustainably, using 67% less energy than traditional methods, and up to 50% faster.
Speed of delivery and climate impact are key, and will become even more so going forward, especially for the healthcare sector, where CBRE expects demand for high-quality real estate to continue growing. In the public sector, the Department for Education and the Ministry of Defence are already leading by example. For instance, the Net-Zero Carbon Accommodation Programme (NetCAP), which Reds10 is delivering for the MoD, relies on precise calculations to achieve a current 43% reduction in embodied carbon and ensure that the buildings will be carbon negative during their lifecycles. The buildings are now harnessing Energy Usage Intensity data to inform ongoing operational efficiency and improvements. These measures have led to them being DREAM ‘Excellent’ and EPC A+ rated.
The rigorous and meticulous design practices of MMC provide visibility and control of all project components, while standardised detailing allows new builds to be based on learnings from past ones. This sets the scene for continuous improvement. Additionally, vertical integration, and the process and programme based approach of MMC, allow for the generation of accurate data that measures climate-related criteria and provide feedback fast into building models. This makes MMC a strong platform to trial innovations and alternative materials.
MMC has already been using advanced digital innovations to a greater degree than traditional construction. As the digitalisation trend evolved during the pandemic, advancing technology will continue to be an important enabler of net zero construction, especially in harvesting data for carbon assessment. The next year will hopefully see more momentum with SMART building technology, which collects data on performance while buildings are in use to generate valuable insights for increasing energy efficiency and cutting emissions.
Looking ahead, I hope to see collaboration in transforming how we assess projects, and key decisions being made based on reliable data. Embracing innovation, including the strengths of offsite construction, will go a long way to building a sustainable future for the industry and meeting challenging climate targets.
If you would like to read more stories like this, then please click here
Related Articles
More News
- £8Bn to be invested in flood defences over the next decade
27 Jun 25
A record £7.9Bn over ten years has been committed to flood defences.
- Boosting British jobs and skills key for firms to win major infrastructure projects
26 Jun 25
Creating high quality British jobs and boosting skills in local communities will be key requirements
- Major rail supply deal to protect thousands of British Steel jobs
25 Jun 25
Thousands of British manufacturing jobs have been secured as the Transport Secretary finalises a major