News - Construction News
Sustainable concrete materials: a novel way to reuse spent tyres
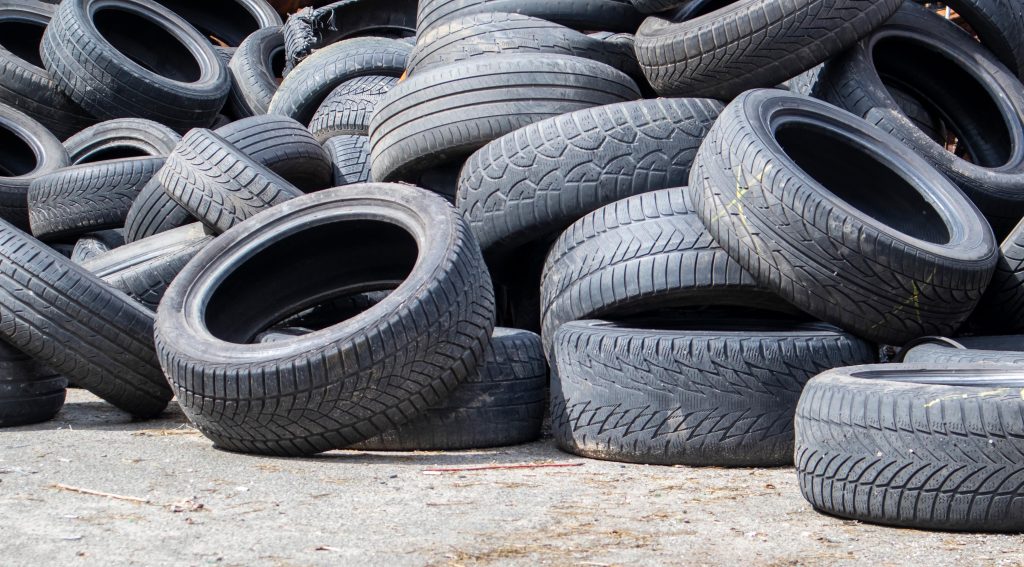
Conventional concrete traditionally used in construction is a robust material, which is reliant on aggregates like sand and crushed stone. However, the mining and transportation of these aggregates contribute significantly to environmental issues, due to energy-intensive operations and resource depletion.
To overcome these challenges, a solution that incorporates recycled elements from discarded vehicle tyres has been introduced. However, the recycling process of vehicle tyres generates a fibrous by-product – about three billion kilogrammes annually – which ends up going to landfill. While some tyre recycling is carried out for applications such as asphalt or playground surfaces, a considerable amount of waste material can’t be used in this way.
The concept of integrating rubber from vehicle tyres into concrete, termed ‘rubbercrete’, has been explored previously. Although, the complexity of vehicle tyres, which consist of diverse materials such as natural and synthetic rubber, fibre, and metal, poses challenges in the recycling process. The current method of recycling involves shredding the tyres, followed by separating the rubber from metal and fibre using magnets and screens. However, some rubber is wasted during the separation process, necessitating a multi-stage separation technique to minimise losses.
Utilities & Civils Solutions has recently been granted a UK Patent GB2600448B for a concrete material that uses recycled material from vehicle tyres as a partial replacement for traditional stone aggregates. A relatively simple production method is required and the solution provides a resilient and effective concrete product.
This novel concrete material comprises two aggregate materials: the traditional mineral elements and the elements derived from the rubber polymer found in spent tyres. The tyre-derived elements which are obtained from shredded tyres, match the diameter of the mineral elements and contain metal sub-elements from the tyre structure.
The method of manufacturing this concrete material involves preparing the mineral elements, shredding the vehicle tyres to obtain tyre-derived elements of corresponding size and combining these elements according to their diameters. This process eliminates the need for excessive sorting or altering the composition of tyre-derived elements before their integration with the mineral elements.
This innovative concrete material not only enhances the flexural strength of the final product, but also offers significant environmental benefits. By reusing shredded tyre fragments as a substitute for stone aggregates, the technology contributes to reducing landfill waste, mitigating greenhouse gas emissions and decreasing demand for stone aggregates. Furthermore, this technology proves highly effective in filling voids or stabilising structures prone to movement, such as mine shafts, sewers, or building foundations. Its natural resilience and ability to bond effectively with cement offer long-lasting properties, making the material a sustainable choice for construction applications.
This new concrete material demonstrates how effective innovation can be in addressing environmental concerns while offering durable and effective solutions for the construction industry. With patent protection secured, Utilities & Civils Solutions benefits from an exclusive right to bring its invention to market and, potentially, license it to third parties. This period of exclusivity extends for up to 20 years, preventing competitors from copying the technology during this time.
Mark Sugden, partner and patent attorney in the Advanced Engineering group at European intellectual property firm, Withers & Rogers.
If you would like to read more stories like this, then please click here
Related Articles
More News
- Homes England acquires Ripon Barracks from MOD
3 Jul 25
Homes England has acquired land at Ripon Barracks which will be developed into 1,300 new
- University joins forces to address critical construction and housebuilding skills gap
2 Jul 25
The University of Salford is collaborating with Cube Thinking to support Barratt Homes in bridging the shift in skills requirements.
- Merit Appointed to NHS Shared Business Services Modular Building Framework
1 Jul 25
Merit is pleased to announce its successful appointment to the NHS Shared Business Services (NHS SBS)