News - Construction News
To create value in the system, we must fix the Apprenticeship Levy now
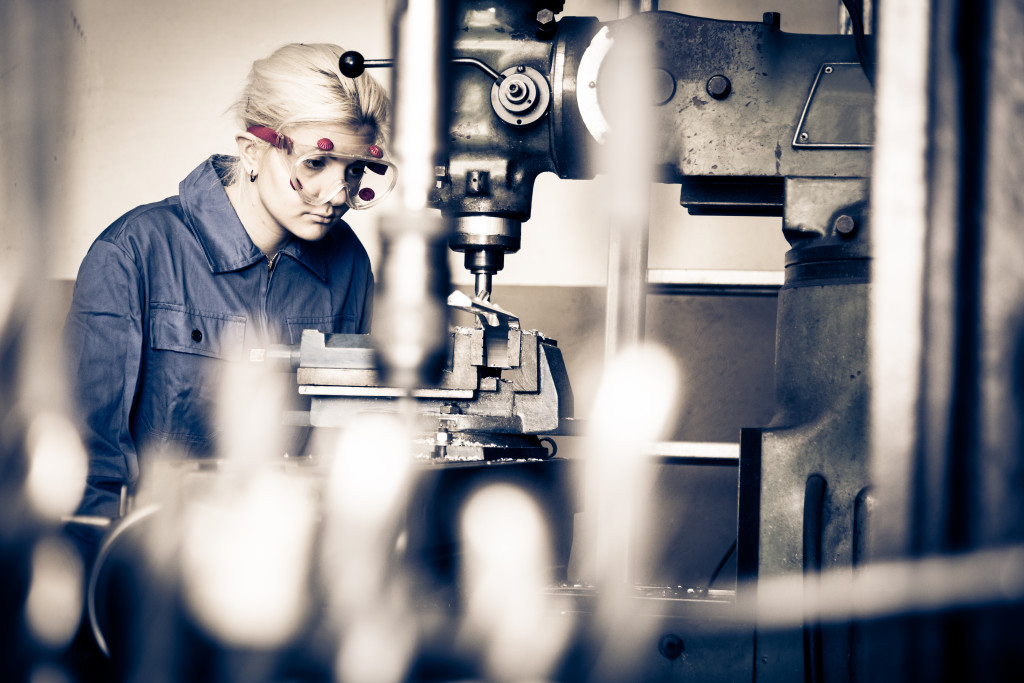
In this article, Verity Davidge, Head of Education and Skills Policy at EEF, the manufacturers’ organisation, talks to UKCO about the problems and solutions for manufacturers presented by the Apprenticeship Levy.
Manufacturers have always been true champions of Apprenticeships
Apprenticeships have been ingrained within the manufacturing sector for decades. Only five per cent of EEF members have never offered apprenticeships. The majority are doing so, and the remainder in the process of doing so. They are one of the key ways manufacturers secure the skills they need for the future. They are also a key channel to get more young people into manufacturing. Indeed seven in ten manufacturers say raising awareness of apprenticeships will get more young people into the industry.
It is this passion and enthusiasm for apprenticeships that so many manufacturers have, that has led us to stand firmly behind the Government’s ambition to get more employers investing in high quality apprenticeships.
The Apprenticeship Levy had laudable aims but has failed to deliver
EEF recently published a report makes the case for unravelling and addressing the alarming drop in apprenticeship starts since the introduction of the Levy and then looking at positive solutions which are on the table to make the Levy work for employers and learners in the long term.
The report found that, whilst the Apprenticeship Levy had laudable aims, what should have been a win-win situation has turned into a lose-lose including for those sectors such as manufacturing and engineering which have been true champions of high-quality apprenticeships for decades.
The headline figures say it all, with continuous falls in starts each month in comparison to pre-Apprenticeship Levy years. And whilst there appeared to be green shoots emerging – more apprenticeship standards and higher level apprenticeships being created, other reports such as that from Reform have put a big question mark over quality too.
When skills shortages are rife companies cannot afford to stop training
Manufacturers cannot afford to stop training apprentices altogether. How can they when three-quarters of manufacturers (according to the report) are concerned about their company’s ability to access the skills they need? Add to that an ageing workforce, Brexit and a fast-moving industry where new technologies are changing the way firms work as well as the skills they need.
Where possible, manufacturers have powered through what has been a costly and complicated programme of reform. That said, one in ten have either delayed or cancelled an engineering apprenticeship specifically because of the Levy.
These are apprenticeships that could have been created, these are opportunities that could have been available to young people, but because of the complexity and rigidity of the Apprenticeship Levy and wider reform programme, they have been cancelled or put on hold.
We need to add value in the system. If we haven’t added any value, then what was the point of this radical reform?
The Government has not delivered on the Levy’s initial promises to employers.
In one of the (many) consultations the Government has published following the Richard Review of Apprenticeships, the Government made promises about the Levy to employers: the Levy will be simple; the Levy will be fair; the Levy will allow employers to get back more than put in; the Levy will give employers real control.
On hearing this, manufacturers bought in to some aspects of the Levy. While over a third of companies saw no benefits to the Levy, some saw silver linings in the form of greater purchasing power to buy the provision they needed and the opportunity to create more apprenticeships in their businesses.
But these promises have been broken. Our report highlights the stark difference between the Government’s “vision” and manufacturers’ “reality.” Manufacturers have faced challenges at every step of their Apprenticeship Levy journey.
Rushed reform and an inflexible system have created problems
Manufacturers’ frustrations about the Levy aren’t driven solely by the fact the Levy is a tax, but rather by the frustration that the Apprenticeship Levy has not helped them to create more quality apprenticeships.
The reforms were rushed in. Manufacturers felt unprepared and received key information too late. Forcing the introduction of the Levy too quickly has also had implications for the wider Apprenticeship system. According to the EEF report, over half of manufacturers said that standards were not ready for delivery – and those were the lucky ones who managed to find firstly a relevant standard and secondly a provider willing and able to deliver it.
Then there are the funding rules themselves, which are complex and inflexible.
For example, some manufacturers don’t recruit on an annual basis because they have just 24 months to spend their Levy funds. Many companies, particularly SMEs, will only recruit apprentices every two to three years, so are immediately put at a disadvantage.
There is also a cap on the amount a Levy payer can spend (of what was supposed to be their own money!) The absolute maximum for the very best, most expensive apprenticeship is £27,000. This is supposed to cover training costs and assessment. But it takes no account of the huge on-site costs and additional costs manufacturers incur to get the apprenticeship training they, and the learner need. In fact it’s not uncommon for manufacturing employers to say for every £1 of the Levy they are spending £4-5 again out of their pockets.
This is just a snapshot of some of the challenges.
Solutions to save the Apprenticeship Levy
According to the EEF report, 95% of manufacturers want to see some form of change in the Apprenticeship Levy. Only 5% want to leave it as it is.
The majority (52%) want to see improvements made, 26% want to see the Levy evolve into a wider training Levy payable by all business and 17% want to scrap the Levy completely.
The mandate from the industry is to save not scrap. But we need to save it now. We cannot wait around in the hope that the numbers might pick up. EEF has been clear on what must now happen to the Levy to get it back on track. We are recommending that the Government:
- Move the Apprenticeship (Levy) Budget from Department Expenditure Limit (DEL) to Annually Managed Expenditure (AME)
- Increase the time that employers have to spend their Levy funds to at least 48 months
- Review the funding band structure, removing the upper limit
- Expand incentive payments to employers, providers and learners for STEM apprenticeships
- Increase the amount of unused funds employers can transfer to over 50% and remove restrictions on transferring to a single employer
- Allow employers to agree a payment schedule with their provider
- The process of signing off standards must become quicker and more transparent and empower the role of employers further
Getting apprenticeship policy, and wider education and skills policy right is more important than ever as the UK prepares to leave the EU. Manufacturers are committed to playing their part but Government must act now and fix what is clearly broken in the system.
If you would like to read more articles like this then please click here.
Related Articles
More News
- Building the next generation
17 Jul 25
We are facing a skills crossroads in our industry, says Richard Martin, Managing Director, Churngold
- Plan to kickstart onshore wind revolution
17 Jul 25
Onshore wind is set to accelerate over the second half of the decade.
- Homes England supports Greencore Homes with new sustainable homes
16 Jul 25
Homes England will provide funding to support the delivery of Milton Heights.