News - Construction News
Decarbonising cement production
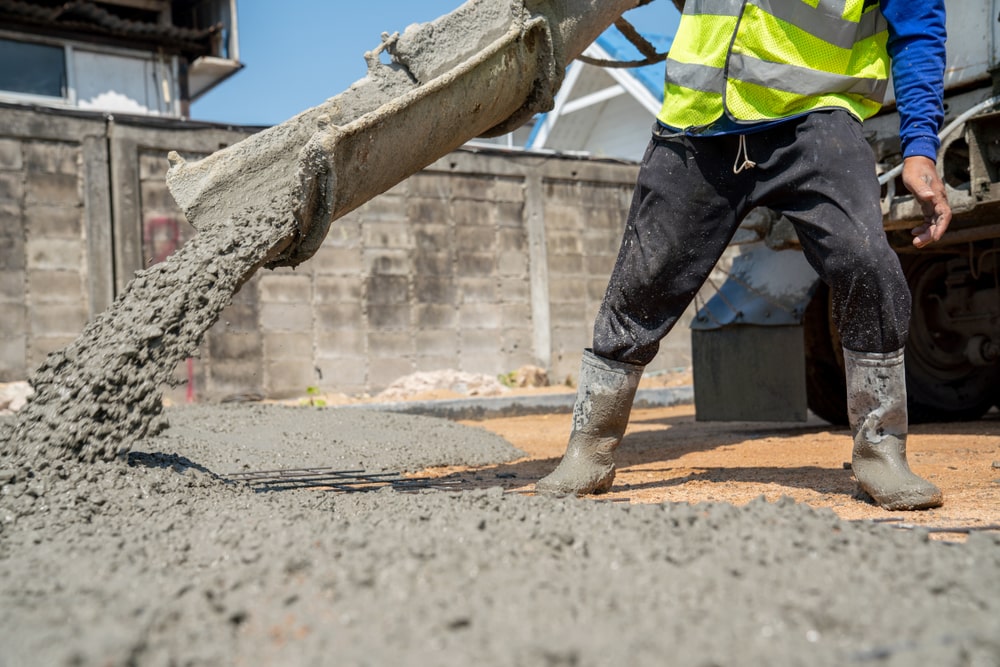
COP26 has elevated the debate once more: the buildings and construction sector need to quickly decarbonise to achieve net zero. The industry itself has a vital role to play in lowering emissions. A study by the International Energy Association found that the buildings and construction sector accounted for 36% of final energy use and 39% of energy and process-related CO2 emissions, with 11% of these emissions resulting from manufacturing building materials and products such as steel, cement and glass.
Philipp Furler and Gianluca Ambrosetti – CEOs and co-Founders of Synhelion, talk us through the construction industry’s ambitions for net zero and the role cement will play.
We need to lower emissions fast
Producing cement is one of the most CO2 intensive activities. One-third of cement-related emissions come from the burning of fossil fuels to heat the kiln. The other two-thirds stem from chemical reactions that release CO2 when limestone is processed. To achieve net zero and meet global commitments such as the Paris Climate Agreement, there is no way around decarbonising the cement industry. It’s a twofold challenge, though technological solutions can help to solve it.
Using solar energy instead of fossil fuels
In existing cement plants, fossil fuels are burned to generate the required high-temperature heat in the cement kiln. How can the cement industry switch to renewables? The solution to this challenge is actually pretty obvious – the sun. Concentrated sunlight can in principle reach any temperature required by man-made processes. Solar heat is the most abundant renewable energy resource on earth. In fact, the sun delivers more energy to our planet within a couple of hours than the whole world consumes within a year. The challenge lies in harnessing this huge energy potential in an efficient and economic way.
Companies such as Synhelion have done that and developed proprietary solar technologies that generate the required high-temperature process heat from concentrated sunlight. The generated heat is primarily used to produce renewable synthetic fuels that can be used for applications such as powering aircraft. However, the solar heat can also be applied to other industries that require high-temperature process heat, like the cement industry. Heating the kiln using only the power of the sun could potentially mitigate one-third of the emissions produced in the cement manufacturing process.
Recycling unavoidable emissions
But what about the other two-thirds of emissions that are released when limestone is processed? Since CO2 is a product of the chemical process, its formation cannot be avoided. However, it’s possible to capture the CO2 and recycle it instead of simply releasing it into the atmosphere. The CO2 produced in cement production can be captured directly in the process of its creation by modern carbon capture technology. Once the CO2 is captured, it can either be stored or used to produce synthetic fuels, for example.
How does it work in practice?
A field of mirrors concentrates solar radiation at a focal point at the top of a solar tower. At the focal point a solar receiver is located. When the sun shines, the concentrated sunlight heats the heat transfer fluid (HTF) inside the solar receiver to up to 1’500°C. The heated HTF is transported to the ground, where it delivers the high-temperature solar heat to the cement pyroprocessing. The system also includes a thermal energy storage to ensure continuous, uninterrupted cement production, even when the sun isn’t shining.
And now comes the cherry on top: The gaseous HTF is composed of CO2 and H2O, which circulates in a closed circuit. The CO2 emissions from the limestone processing mix with the HTF, creating a concentrated stream of CO2 and H2O and massively simplifying CO2 capture.
The cement industry on the road to net zero
By replacing fossil fuels in cement plants with high-temperature solar heat, manufacturers can capture 100 per cent of CO2 emissions, which can then be utilised as feedstock for fuel production. This radically new approach will enable cement manufacturing to achieve net zero.
This switch is already happening. CEMEX, the second largest building materials company in the world, is already planning to adopt a staged approach towards implementing the technology. A pilot installation is expected to be incorporated into one of the company’s existing cement plants by the end of 2023 and gradually be extended to a fully solar-driven plant.
Ambitious new technology will be a major contributor to solving the climate crisis and lowering the CO2 emissions of the buildings and construction industry. Together, technology pioneers such as Synhelion and established market players like CEMEX can collaborate to close the carbon cycle and enable the industry to accelerate the pace towards achieving net-zero emissions.
Author: Philipp Furler and Gianluca Ambrosetti – CEOs and co-Founders of Synhelion
If you would like to read more stories like this, then please click here
Related Articles
More News
- Merit Appointed to NHS Shared Business Services Modular Building Framework
1 Jul 25
Merit is pleased to announce its successful appointment to the NHS Shared Business Services (NHS SBS)
- £1Bn backed renewal of broken bridges, ruined roads and tired tunnels
30 Jun 25
The Structures Fund will inject cash into repairing bridges, flyovers and tunnels across Britain.
- £8Bn to be invested in flood defences over the next decade
27 Jun 25
A record £7.9Bn over ten years has been committed to flood defences.