Sector - Modular
Patent of the Month – hybrid housing solutions
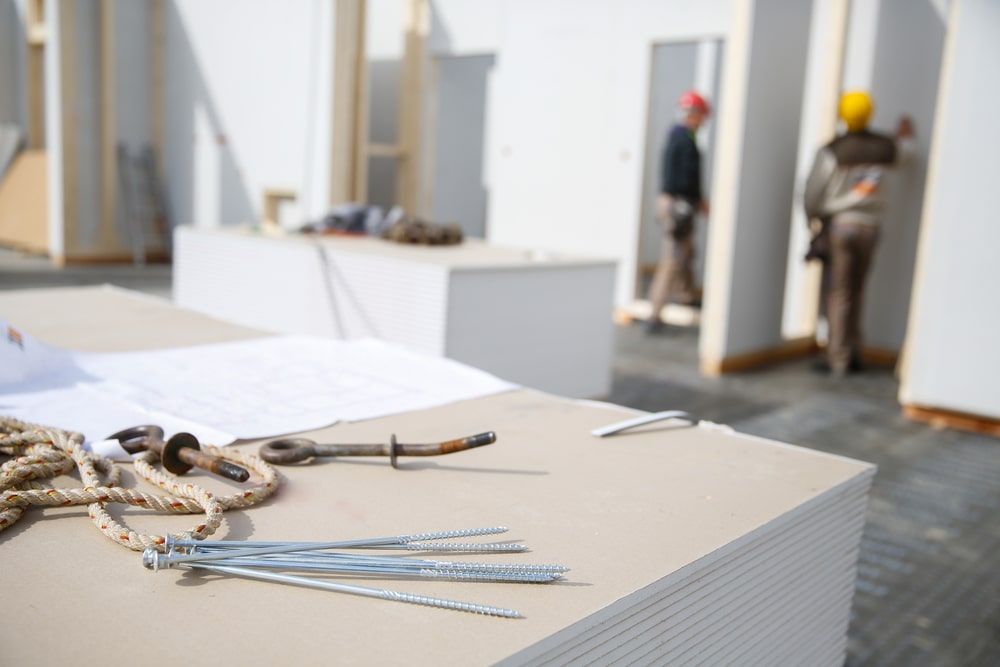
Breaking the mould: innovating hybrid housebuilding solutions
Despite demand for residential property continuing to outweigh supply of housing stock in the UK, few advancements have been made in the methods used to build new homes.
Although housing built using traditional methods have a long lifespan, they can be slow to construct and often require the use of expensive materials that are not sustainable and have a considerable impact on the environment. There is therefore a growing need for innovative solutions to facilitate faster construction of housing and meet sustainability standards.
Modern methods of construction focus on off-site construction techniques such as mass production and factory assembly. Prefabricated buildings are made from modules that are assembled offsite and then transported to the site of the development. However, methods used to construct modular houses often require the storage and transportation of large modules, which can be costly and create issues if there is a lack of space.
Another potential solution uses prefabricated structures to connect panels or frame-type modules. However, even this solution has disadvantages, as the prefabricated components can only be connected once they are onsite.
UK based start-up, Sano, is an innovative company, specialising in modern methods of construction. Recognising the importance of intellectual property protection, Sano has recently been granted a UK Patent – GB2606863 – for a novel, hybrid method of construction.
The patented technology involves the use of a first building section, which is constructed onsite, and a prefabricated module, which is constructed offsite.
The first building section includes upper and lower storeys. The prefabricated module is transported to the site and connected to the first building section, and both form the perimeter walls of the hybrid house.
This construction method is advantageous because the first building section can be constructed to a nearly assembled state, and the prefabricated module transported and connected with minimum delay. This negates the need to store the prefabricated module onsite for extended periods, which can be expensive.
Additionally, construction is both simplified and accelerated because the building section and the prefabricated module can be constructed separately and independently, and then connected together.
Sano has demonstrated its patented technology through the creation of M-DOCK houses. The houses are fully customisable, with the ability to choose from a range of materials for both the first building section and the prefabricated modules. The prefabricated modules are QA approved and can be assembled offsite to include a number of features including bathrooms, doors, stairs and boiler.
With patent protection secured, Sano will benefit from an exclusive right to bring its invention to market and, potentially, license it to third parties. This period of commercial exclusivity extends for up to 20 years, during which time competitors are barred from copying the innovation.
Mark Sugden, partner and patent attorney in the Advanced Engineering group at European intellectual property firm, Withers & Rogers.
If you would like to read more stories like this, then please click here
Related Articles
More Modular News
- BSI publishes groundbreaking standard for MMC in residential developments
28 May 25
New specification to build confidence in modern methods of construction (MMC) for residential developments has
- Wellbeing sacrificed for profit
23 Oct 24
A new report by the APM calls for greater strategic leadership to improve employee wellbeing
- Why Modular Construction in the Commercial Sector Stacks Up
15 Apr 24
Richard Hipkiss, Development Director of the MPBA, considers why the outlook in mature commercial markets