Sponsored
The manufacturing process for rubber extrusions
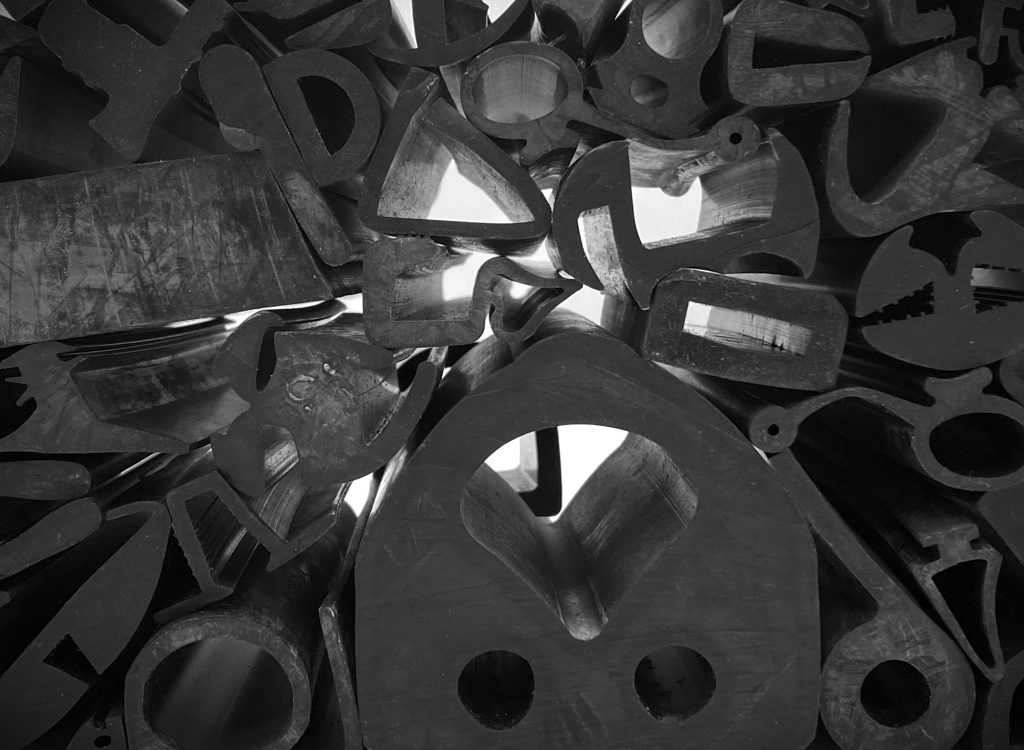
Rubber extrusions are important to the construction industry, providing essential functions such as sealing, insulation and safety production. These components are essential for ensuring the durability and efficiency of building and infrastructure projects. The manufacturing process for rubber extrusions is a comprehensive sequence of steps that helps ensure the final product meets specific performance and quality standards.
This article from Seals Direct explains the steps involved in manufacturing rubber extrusions, with a particular focus of the requirement for their applications within the construction sector. From the selection of base materials to the final finishing touches, each phase of the manufacturing process contributes to the creation of high-quality rubber extrusions that support the diverse needs of the industry.
Selection of Base Material
The manufacturing process begins with selecting the appropriate base material. The widespread availability of various rubber compounds, such as EPDM, neoprene and silicone, allows us to choose a compound that meets the specific requirements of the application. For the construction industry, properties like temperature resistance, flexibility and environmental resilience are important to ensure a long lasting sealing solution. The choice of base material is foundational as it dictates the subsequent qualities and applicability of the final extrusion.
Compounding
Once an appropriate rubber compound has been selected, the compounding phase begins. This involves mixing the base rubber with a range of chemicals and fillers, such as curing agents and accelerators. These additives ultimately define the density, elasticity and other mechanical properties of the rubber. Precision in compounding is important to ensure consistent quality and performance of the final extruded rubber product. This is important for its application in construction where reliability and durability are paramount.
It is also possible to add blowing agents such as azodicarbonamide and sodium bicarbonate into the compound. This allows us to manufacture sponge rubber seals for applications that require a compressible material.
Extrusion
Following compounding, the rubber mixture is then fed into an extruder. During this stage, the mixture is heated and forced through a die shaped according to the profile of the desired extrusion. When activated by heat, the blowing agents release gases that cause the rubber compound to expand and form a cellular sponge-like structure. This expansion is controlled to meet the specific dimensions and shapes required for various applications, such as weatherstripping and other glazing seals.
Curing
After extrusion, the rubber section needs to be cured to set its shape and properties. Curing involves a continuous vulcanization process which often involves salt baths or hot air tunnels. This step cross-links the rubber molecules, solidifying the extrusions structure and imbuing it with strength, elasticity and dimensional stability. For construction based projects, cured rubber extrusions must maintain their integrity and performance under various environmental conditions, including exposure to moisture, temperature fluctuations and mechanical stress.
Cooling and Finishing
Once cured, the extrusions are cooled and cut to specific lengths or coiled. They may also undergo additional finishing touches, such as flocking or the application of adhesive backing. This stage is essential to prepare the rubber extrusions for direct application in various construction products.
Applications in the Construction Industry
Rubber extrusions are used extensively in the construction industry due to their versatility and reliable performance. Key applications include:
- Weatherstripping: Providing airtight seals around windows and doors to improve energy efficiency and protect against weather elements.
- Expansion Joints: Absorbing thermal expansion and contraction in buildings, bridges, and roadways to prevent structural damage.
- Gaskets and Seals: Ensuring watertight and dustproof connections in various construction assemblies, from HVAC systems to plumbing.
The manufacturing process of rubber extrusions, from selecting the base material to compounding, extrusion, curing and finishing ensures that these rubber components meet the high standards and accreditation required in the construction industry. By providing essential properties such as flexibility, resilience and durability, rubber extrusions play an important role in enhancing the performance and longevity of construction projects. Understanding this process underscores the importance of precision and quality in producing materials that support the infrastructure and building sectors.