Sector - Consultancy
Time to Start Boxing Clever with MMC in 2021
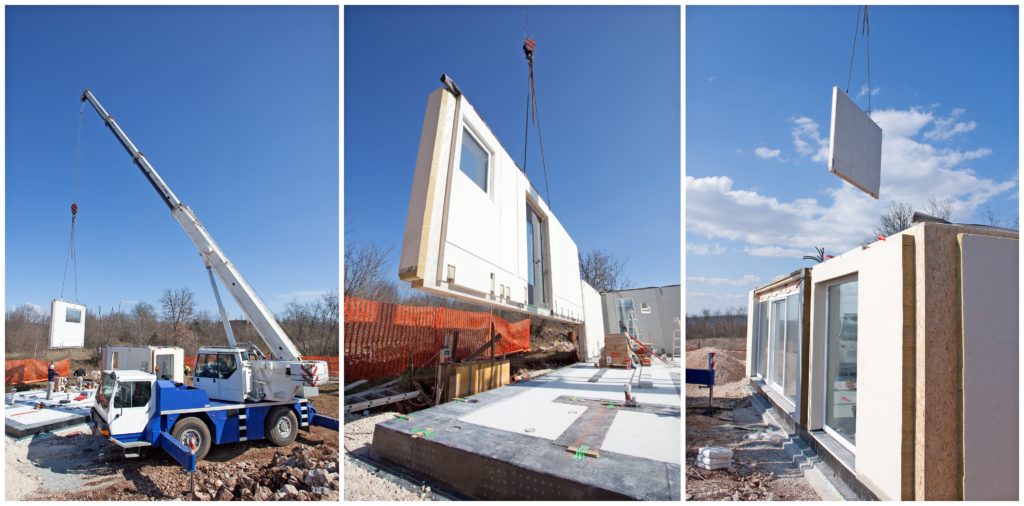
In this latest feature, Anthony Lymer, business development manager at Protrade, which analyses the pros and cons of MMC in 2021 and why it is time for the sector to, essentially, to start boxing clever.
MMC, otherwise known as Modern Methods of Construction, is a wide term.
It covers a range of offsite manufacturing and on-site techniques that provide alternatives to traditional house building methods.
Off-site construction allows most construction phases to be undertaken simultaneously, all while site preparation, foundations, and utility connections are being prepared. Whole completed units can be built in a factory ready for final assembly and finishing in situ.
There is already a significant level of engagement with MMC across the housing development sector, from existing house builders and housing associations, through to SME’s setting themselves up specifically to exploit opportunities in MMC.
However, construction doesn’t stop at residential properties – other important sectors include educational, social housing, custodial, health, and the hotel industry.
In 2019 alone, millions of pounds worth of investment from both the UK Government and overseas were poured into creating linear processes for cost-efficient, safe, and sustainable manufacture.
With the huge demand for housing seemingly unachievable using traditional methods, MMC is widely recognised as a viable option to alleviate those demands.
So, what are the benefits of MMC?
Designing purpose-built production lines using a linear process has allowed manufacturers to cut costly time from fabrication which, in turn, allows the investment in sales and rent to be realised much quicker.
Many manufacturers already operate two shifts and 24-hour production is a thought that is not too far away from becoming reality now.
Another important factor in construction costs in the UK is our exceptionally adverse weather conditions.
Delays in meeting completion dates and the resulting penalties are almost an accepted part of the process in traditional building and one which offsite manufacturing largely avoids.
Although appearing almost daily in our news feeds, the climate change crisis, renewable energy, and sustainability have held a magnifying glass up to construction for many years now and the pressure for creating energy-efficient, low carbon emission sustainable buildings has never been so focused.
Innovative technology in MMC is making regular advancements in the fight to reduce our ecological footprint. Reducing vehicle movement also minimises disruption to local residents, road congestion, and carbon emissions.
One of the bigger benefits is the controlled factory process, which drives a highly consistent quality finished product with minimal defects.
Buildings are scrutinised to the highest standards prior to delivery and it’s not unusual to drive past a plot one week and find a completed property with a family car in the driveway the next!
Finally, it will also come as no surprise that construction is one of the most dangerous sectors to work within.
HSE reported 30 deaths in the construction industry 2018/19, 49% of which were as a result of falling from height. Safety measures are easier to implement and monitor within a factory setting, as opposed to a large open plan construction site.
What are biggest challenges facing MMC?
Bringing change to the traditional processes of construction is clearly a slow burner but disruptors to the market have already proved that high quality, insurance accredited products can be manufactured to increase the adoption of offsite and pre-manufactured solutions.
It’s also important to ensure a continual raised awareness of the already established benefits of offsite versus traditional.
It’s not what some would deem a ‘fad’. Millions of pounds worth of investment validate that but the message needs to be repeated.
The UK Government has previously issued calls for more builders to embrace the process, which has been supported by numerous factory visits from the former housing minister, Esther McVey, as well as her predecessor, Kit Malthouse.
But supply chains must also improve their systems by adapting to the demands of fast consumed materials. If millions are being spent to create a linear production process, shouldn’t this also apply to lean purchasing habits? Many companies are still purchasing supplies in a traditional manner.
We also have the B-word to consider…
While most people must be fed up with the events in politics over the last three years, it would be wrong to dismiss the possible ramifications of the UK withdrawal from Europe.
With Brexit now in the process of being implemented, the potential for labour/skills shortages may further drive the adoption of MMC, which can benefit greatly from its build flow processes.
So, who are the influencers behind the change?
There are a few.
The Government, housing associations, contractors, architects, trade organisations, and manufacturers are all obvious influencers for disruptive change but there is another to consider.
Public purchasing.
With a social or economic conscience, they too must also be informed of the benefits of this industry.
Such is the high quality of design already out there, it would challenge many passers-by to say for certain whether that building was traditionally or offsite built and if we adhere to the duty of care we have for the future – and in fact, the present – needs, we must embrace the opportunity to change.
If you would like to read more stories like this, then please click here
Related Articles
More Consultancy Features
- Outlook for the property and construction sector heading into 2025
17 Dec 24
Across the residential, rental and infrastructure sectors, there will be many challenges in 2025, as well as many opportunities.
- No compare – why framework comparison is a risky business
23 Jan 23
At a time when the framework market is more competitive than ever, it can be tempting for public sector organisations to choose the lowest cost.
- Physics engineering to go mainstream in 2022
8 Feb 22
Building physics engineers will become mainstream during 2022.