Sector - Software & Technology
Using Virtual Technology to Build Back Better
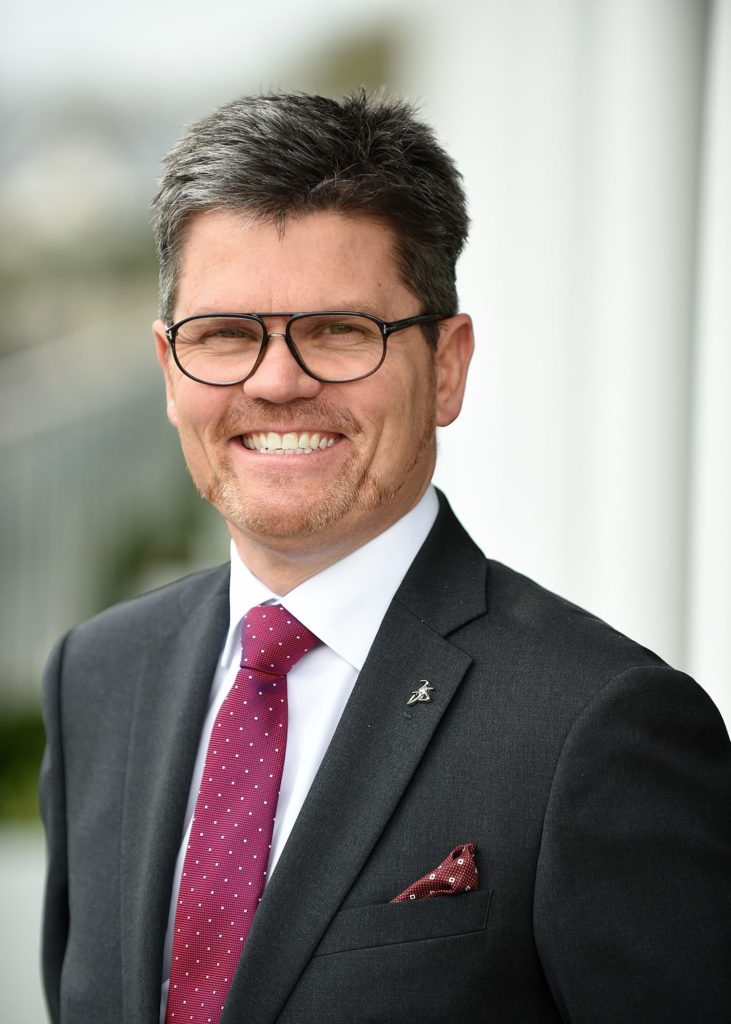
John Kitchingman is Managing Director of EuroNorth for Dassault Systèmes. In this latest feature for UKCO, he writes about the construction sector using virtual technology as part of the UK Government’s ‘Build Back Better (and Greener)’ campaign.
As the construction sector recovers from the double-whammy of COVID-19 and the recession, it is vital that it recognises that its traditional processes are no longer fit for the modern world and need a radical overhaul. The construction industry has faced a difficult year causing major problems for the sector. At the beginning of the first national lockdown, many construction sites were forced to close and construction output saw its sharpest decline in recent memory. This did improve and as lockdown measures started to lift, UK builders reported their strongest monthly rise in activity in almost five years in July. The Prime Minister has also placed the construction industry at the centre of his government’s “Build Back Better (and Greener)” campaign.
The global construction industry is estimated to be responsible for between 35 to 45 per cent of CO2 released into the atmosphere, making it a major contributor to global warming. Given the UK’s commitments to reduce greenhouse gas emissions and fight climate change, the industry urgently needs to adopt more sustainable methods. Virtual technology and a data centric approach are key to ensuring the sector recovers in a sustainable way.
Using data to create efficiencies
Pre-lockdown, around 35% of construction projects ran over budget. This leads to massive waste of resources, including materials and money, leading to many project owners looking for ways to become more efficient. These project owners need a design and construction process that puts as much focus on meeting the budget as it does on the lifecycle costs of the physical asset.
These long-term cost and material savings depend on data. The development and maintenance of a physical asset from design through fabrication to operation and maintenance can only be managed with accurate data that sets a baseline and clear trajectory for improvement. Data is at the heart of process improvement and expected at every stage of the project.
This increased use of reliable data will help the sector to reduce waste and to boost the quality from design to construction, for instance, defining modular assembly components integrated in a variety of product lines. Modularity will allow to address the complexity of upcoming projects while addressing increasing customization and sustainability needs, as well as match high market variability.
Digital twin technology
A digital twin is a virtual version of a process, product or service, which creates a two-way link between the physical and virtual world. The twins work by interrelating data and controls from across an entire eco-system, collected via platforms, databases and sensors and allowing it to interoperate. Digital twins also rely on statistics, machine-learning and artificial intelligence to understand and predict the operational state and behaviour of the real-life product or process.
Several industries are already benefiting from digital twin technology, including automotive, manufacturing, and most recently healthcare (see the Living Heart project as an example). Digital twins are also particularly useful for the construction industry because it requires real-time information to drive down costs, as well as boosting efficiency and productivity. The main benefit in construction is using digital twins to test virtual construction sequencing and logistics scenarios, which can lead to reduced construction and operating costs. Digital twin technology can also collect and monitor real-time data to optimise a building’s operational performance and sustainability, which can help to reduce the sector’s carbon footprint.
It is also worth mentioning that the most costly problems within the sector often appear once construction stops and commissioning begins. Many construction companies still traditionally perform commissioning with clipboards and a paper list of parts. Manually executing the commissioning phase this way wastes a considerable amount of time and requires more engineers to complete, in line with aggressive project timeframes. By leveraging digital twin technology, companies are able to generate digital commissioning procedures based on the digital twin model. Commissioning engineers are able to update the virtual twin in real time with onsite data, using mobile access via tablets for instance. This a crucial way to significantly improve on-site collaboration and de-risk projects.
Going beyond this, it is possible to connect the twins of different buildings and their construction sites with layers of infrastructure to benefit from the insight of a system of systems. This allows the industry to be able to create ‘smart cities’ as designers and town planners can interrelate event-driven data to gain insights into a ‘living’ city. Scenarios such as the impact of a new building on traffic flow or water and power supplies can be simulated to gauge how to go forward with town planning and put in place the appropriate measures to improve quality of living and help combat the effects of climate change, for instance.
The best way for the sector to become more sustainable is by embracing virtual technology and digital transformation. It is time to do for infrastructure, construction and cities what we’ve done for manufacturing, by taking a life-cycle style approach and leveraging digital technologies such as 3D visualisation for a true digital renaissance of the built environment.
If you would like to read more like this, then please click here
Related Articles
More Software & Technology Features
- Alternative building practices are crucial to unlocking AI infrastructure benefits
7 Mar 25
With AI capabilities developing at an unprecedented pace, the government has announced its AI Opportunities Action Plan.
- Reflections and predictions: Leading professionals discuss the year ahead for 2025
3 Feb 25
Leading industry experts give their perspectives on the key trends poised to define 2025.
- AI to move from a tactical tool to a strategic priority for real estate industry
9 Jan 25
Adoption of AI in real estate will tip over from tactical usage to a strategic priority in 2025.