Sector - Finance & Legislation
Three Steps SMEs Can Take to Manage Supply Chain Disruption
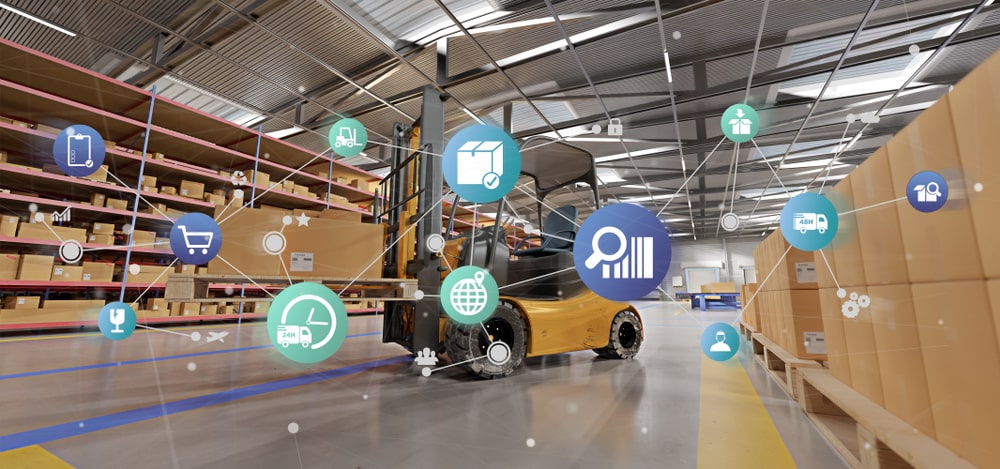
Tim Boag, group managing director of business finance for Aldermore Bank, writes about how UK SMEs can mitigate supply chain disruption post pandemic.
As the UK and other major economies around the world emerge from the Covid-19 pandemic, many businesses which were completely closed during national lockdowns are now dealing with a surge in demand. Consumer demand and signs of confidence among SMEs are returning, construction companies have recorded an increase in output in August and activity has continued to expand for the past seven months, according to the latest Construction PMI data1. Research from Aldermore also found confidence among SMEs has increased, as they plan to invest more into growing their business over the next 12 months, rising 190% to £283,5002 up from £97,719 in February3.The impact of the ongoing material and skilled worker shortages however has hampered activity. Delays at ports as a result of Brexit, in addition to the current haulage crisis has only exacerbated this issue. In August, the Construction PMI reported that the sector experienced ‘severe’ supply chain disruption and the second-fasted rise in input prices recorded as companies now face an additional financial burden to their business.
We recognise the challenges construction SMEs face as they look ahead and confront a fresh range of issues following the pandemic. Outlined below are three steps SMEs can take to ease stock shortages and supply chain pressures, including: building a supply chain map, strengthening relationships with suppliers, and automating parts of the supply chain process.
Create a supply chain map to mitigate the impact of risks ahead of time
Globalisation has enabled just-in-time delivery systems, where manufacturers receive goods just as they need them for the production process. When it works, this system can reduce inventory costs and improve efficiency for businesses. Yet just-in-time delivery relies on consistent suppliers and porous borders which have all been placed under major strain due to the pandemic, Brexit, a shortage of lorry drivers and events such as the blockage of the Suez Canal.
Regardless of whether your business uses a just-in-time delivery system or not, it’s worth creating a supply chain map which showcases the full picture of your supply chain network. This will make it much easier to visualise where potential change is needed if one supplier faces a shortage or if there’s a surge in demand for a particular component. Supply chain maps also allow you to analyse the connections between entities in the supply chain, meaning you can spot where delays originate from and focus on fixing them.
Develop relationships with your supply chain to collaborate better with them
Whether your supply chain includes multiple vendors across several continents or just one or two local suppliers, it’s important to build strategic and mutually beneficial relationships to mitigate supply chain risk. Get to know your suppliers better, learn how they work, how they prefer to communicate and the technologies they use in their line of work. If possible, try to identify key stakeholders in your supply chain to negotiate with as this could make it easier to amend certain processes and plan for contingencies.
When building an initial relationship with a supplier, don’t focus too much on the fee they’re asking but instead concentrate on the quality of the product or service on offer. Prioritizing value and long-term success over costs will benefit your business in the long run.
Automating parts of your supply chain process can increase productivity, efficiency, and accuracy.
Using machine learning or artificial intelligence in your supply chain might sound farfetched but supply chain automation doesn’t have to be overly complicated. Automation is about identifying repetitive tasks that are time-consuming or error-prone and finding ways to automate them. Issues with supply chains can result from human error such as a payments issue or missing documents. Perhaps the most basic form of automation can occur in back-office functions, like invoicing, inventory management and order tracking. Investing in some form of supply chain automation can reduce operational costs, improve customer service, and help optimise your supply chain management.
While there are challenging times ahead for the sector, construction SMEs have already demonstrated their resilience throughout the pandemic and should take the necessary steps to ease supply chain pressures.
If you would like to read more stories like this, then please click here
1https://www.markiteconomics.com/Public/Home/PressRelease/53d8bb43bc3e45cf9be7330c306168fe
2Research conducted by Opinium Research between 6 and 16 July 2021 with a sample of 200 key decision makers in companies with 50-500 employees, in construction, business services, legal services, industrial and warehouse, manufacturing, professional services, real estate and transport or storage.
3Research conducted by Opinium Research between 10 and 25 February 2021 with a nationally representative sample of 1,271 senior decision makers in UK SMEs.
Related Articles
More Finance & Legislation Features
- How sustainability and innovation can help construction companies in limit financial loss
28 Oct 24
Construction businesses are facing many challenges to their bottom line at once, but utilising creative strategies to innovate can help mitigate losses while also committing
- BESA calls for ‘tough and rapid response’ to ISG chaos
25 Sep 24
BESA has urged the government to act quickly in response to the collapse of main contractor ISG.
- Third party red flags: how developers can avoid reputational damage
31 Jul 23
There are a plethora of risks that developers might face when seeking to deliver a project via a third-party contractor.