Sector - Sustainability
I want to make Britain’s roads 90% recycled
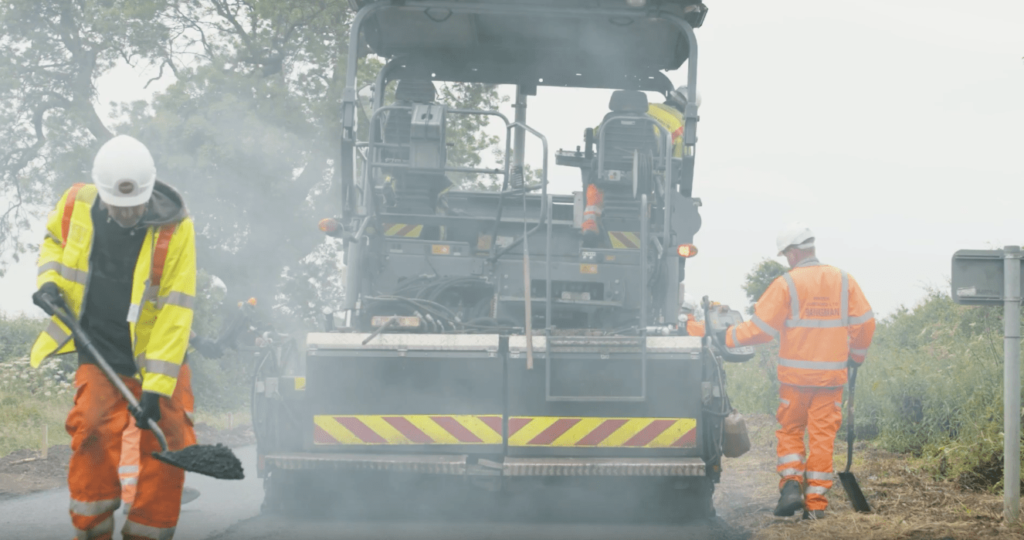
How long will it be before the roads you drive on are almost entirely made from recycled material? We speak to Bruce Spencer-Knott, MD of Minster Surfacing.
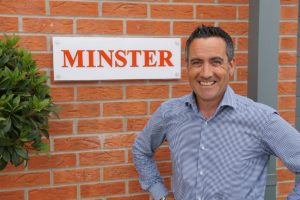
Bruce Spencer
With the wealth of technology that’s now available, there’s no reason why they can’t be and, given the impact that road surfacing has on the environment, they absolutely should be.
As construction materials go, the production of virgin asphalt takes a hefty toll on the environment. Asphalt is made from distilled crude oil and mineral aggregate, two resources that are finite and in short supply in this country and around the world. These ingredients have to be refined, combined and transported long distances, amounting to a significant carbon-cost. Furthermore, as the cost of crude oil rises, so does the cost for road surfacing. Meanwhile, the construction sector is constantly hungry for minerals so the quarries in this country are racing to meet demand while doing what they can to avoid irreparably scarring the landscape.
Depending on traffic and climatic conditions, a well-laid asphalt surface has a lifespan of around 25 years on average, after which it will need to be relaid. This means that just as frequently as we’re laying roads, we’re ripping up old ones, so how much better would it be if we could lay those new surfaces using all the materials that we dig up from the old ones?
Well the technology exists and to an extent, we’re already doing it: My company, Minster Surfacing is routinely recycling old roads to create new ones using the latest technology. We utilise an on-site closed loop manufacturing process developed by OCL Regeneration. With a mobile recycling plant to produce CBGM & Foambase, which are high quality alternatives to hot asphalt and binder course products made using the material we remove from the same location. This technology dramatically increases the amount of material that can be recycled, it cuts waste and it means large quantities of material no longer needs to be transported long distances to where a team is working.
Meanwhile, a significant quantity of the asphalt we can’t produce ourselves is made from secondary aggregates. This aggregate is made using by-products from steel manufacturing instead of using aggregate from quarrying.
Partnering with OCL Regeneration in this way, Minster is now recycling tens of thousands of tonnes of the material we remove from roads and use it on-site to create the new surface which is around 50% recycled on average. The recycled material that we produce can be laid using the same tools and techniques as used for traditional hot asphalt and they are just as hard wearing. Producing this material produces 32% less CO² than the production of traditional hot asphalt and we can use the same process to convert other material that would go to waste, including concrete and rubble, giving us a ready to use supply of recycled material that can create new surfaces.
Using this technology, we can create the material we need as we work, where we work, using the material that we extract from our work. It’s a great thing to see in action with a much lower carbon cost, a considerably reduced reliance on non-renewable resources and it prevents us from sending hundreds of thousands of tonnes of material to landfill.
This use of recycling technology has helped us win a number of environmental and industry innovation awards, but you may be wondering why every other road surfacing company isn’t able to recycle as much, and you may also be wondering why we can’t currently make roads that are 100% recycled.
One of those reasons is a material which used to be used to make roads in this country called coal tar. While coal tar has medical and industrial uses, the environment agency classify asphalt waste containing coal tar as hazardous. Because of this, many companies won’t touch it and so it has to be safely disposed of. That can cost up to £100 per tonne and it means that all of the material goes to waste, even if the coal tar amounts to just 0.1% of the material.
Whichever way you cut it, sending vast quantities of material to landfill is a waste, especially when environmental regulations do allow for the material to be safely reused and recycled. Even material which is over the 0.1% coal tar can be safely re-used in-line with environmental and local authority standards as a base-layer for a new road. Using our recycling technology, we can reuse this material, saving vast quantities of useable product from going to waste, saving the taxpayer money, giving us an almost constant supply of aggregate and reducing the need for more minerals to be quarried and transported.
Around 50% of roads contain coal-tar, so if this responsible re-use of the material is embraced across the industry and by all local authorities, we can dramatically increase the amount of material that we can recycle on our roads.
Another reason why recycling still isn’t the norm on British roads is a wider problem within the industry. I’m constantly impressed by the dedication many firms have to innovation and technology, but while these companies are embracing new ways of working and making great efforts to work sustainably, there are others that aren’t. Overall, there is a perception among the general population that road surfacing is, and always will be, a dirty, pollutive, low-tech industry and people are unaware that there are greener ways of working. This leads to organisations reaching out to any contractor that can lay a surface or choosing the cheapest company on the tender list because they aren’t aware of the high-tech, sustainable alternatives that could bring so many benefits.
As a whole, the innovators need to do more to raise awareness of the fact that road surfacing is very different to the ‘man in a van’ image people have of it. Unless the wider population begin to understand and appreciate the wealth of technology and innovation that’s transforming the industry, trailblazers will continue being undercut by rivals who just get the job done without any regard for recycling or sustainability and this will mean the roads continue to be laid using new material, with large volumes going to landfill.
These are some of the issues that are holding back recycling across the board in road surfacing, but how can we create roads that are 90% recycled?
Currently, it’s still the case that the very top layer of a road should be virgin asphalt to guarantee a smooth, unblemished surface that will meet all local authority requirements, but the 100mm thick base layer and 100mm thick binder course can be almost entirely recycled. If we were able to routinely work to this level, we could eliminate almost all of the waste produced from road surfacing and dramatically reduce the industry’s reliance on quarrying and crude oil. We can even make good use of all the countless tonnes of material that’s been sent to landfill previously and use it to meet our future demand.
While the mobile recycling plants we use enable us to recycle on-site to create CBGM & foamed bitumen material for the base layer and the binder course, we would be able to increase our recycling capabilities further if we were to supplement this with our own asphalt production facilities to produce material that’s up to 95% recycled.
The difficulty in achieving this is in making sure that we can have a guaranteed supply of 95% recycled asphalt pavement (RAP) that’s close to the point of use to avoid the carbon-cost of transportation and which can be commercially viable. This would be a significant investment, but I’m dedicated to using technology to improve the way we work and I’m passionate about the goal of making road surfacing a greener, more sustainable industry so I’m sure that we can do it.
Road surfacing has long been seen as a necessary evil – a dirty, pollutive and resource intensive industry, but I’m confident that we can achieve my ambition of making every road we work on almost entirely recycled and I’m excited by the potential of the latest technologies available.
Road surfacing can be just as high tech and sustainable as even the most progressive parts of the construction sector, we just need the confidence to embrace the technology available and explore new, better ways of working.
If we can achieve this goal of practically eliminating waste and the need for new material, we could make this industry one of the most environmentally friendly parts of the construction sector
The future of the black stuff could be very green indeed.
If you would like to read more articles like this then please click here.
Related Articles
More Sustainability News
- Plan to kickstart onshore wind revolution
17 Jul 25
Onshore wind is set to accelerate over the second half of the decade.
- Homes England supports Greencore Homes with new sustainable homes
16 Jul 25
Homes England will provide funding to support the delivery of Milton Heights.
- £8Bn to be invested in flood defences over the next decade
27 Jun 25
A record £7.9Bn over ten years has been committed to flood defences.