Features - Business
2021: Construction industry predictions
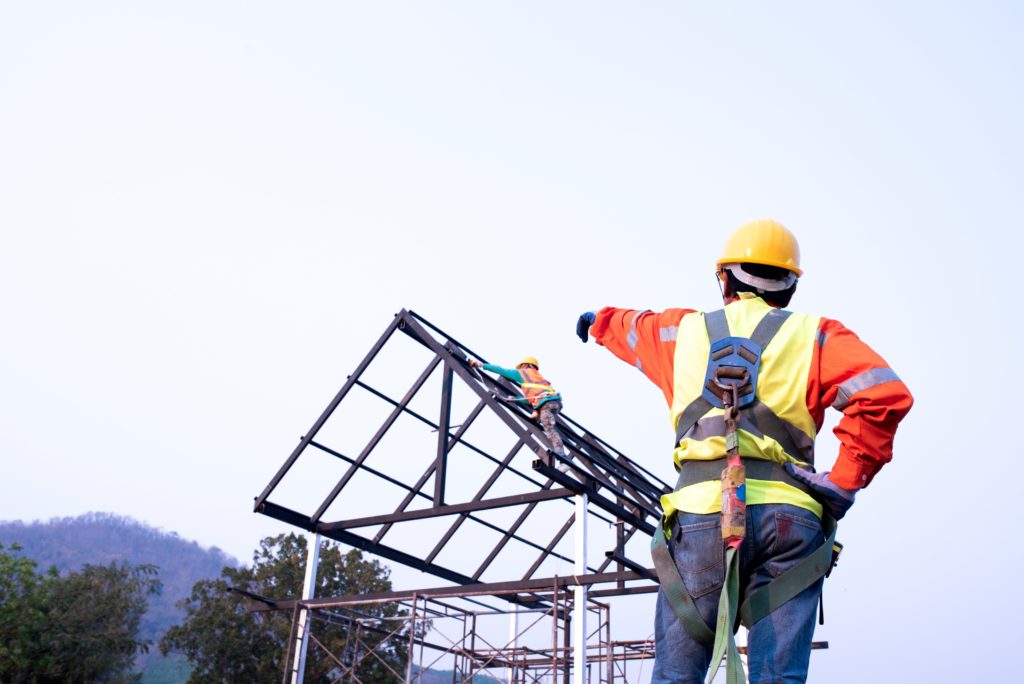
2020 has proven that even that the best laid plans need to be flexible in order to survive. As one of the sectors hardest hit by both Brexit and the coronavirus pandemic, the construction industry has been forced to react, adapt, and innovate. But has this shaped the industry permanently and has it altered what’s on the cards for 2021? Kate Onions, head of construction disputes, and Adam Watson, construction lawyer, both at law firm Shakespeare Martineau, discuss their five predictions for the next year.
Putting the Brexit foot forward
The UK’s existing skills shortage is no secret. With EU talent currently making up eight percent of the construction industry workforce, there is a real concern that the skills gap may increase exponentially (a possible ‘skills gulf’) if EU workers are not permitted to remain in or enter into the UK.
Currently, EU nationals who live in the UK before 31 December 2020 are allowed to continue to do so until 30 June 2021, which is the deadline for applying for settled status. However, any EU nationals arriving after 31 December 2020 will require a visa or sponsorship in order to secure employment.
When it comes to the import and export of goods and materials, there is real uncertainty surrounding how tariffs may be impacted. A change in tariffs for imports, in particular, is likely to lead to the inflation of prices from EU suppliers providing goods and materials to the UK. This is a serious concern given that almost a quarter of construction products used in the UK are imported, with almost two thirds of such products coming from EU countries.
It is good practice, in any event, for contractors to ensure that the channels of communication with their supply chain are open. This will help ensure that when issues do arise there is likely to be good communication and dialogue in resolving the issues without causing pinch points and critical delays to projects.
The impact of Brexit on the planning process could influence development programmes, where consents must be obtained before construction works can even begin. It is therefore more important than ever for contractors to plan ahead and include a buffer zone (i.e., float) into any strategy. However, it is also key to avoid the tendency to try to cover all eventualities and focus on the most important suppliers and the most vital information in any supply chain mapping.
Ongoing impacts of the COVID-19
The biggest impact of the COVID-19 pandemic on the construction industry has arguably been financial. However, one of the most noticeable impacts on a day-to-day basis is the huge increase in on site safety, something which will continue to develop and increase during 2021 and beyond.
In order to mitigate the spread of the virus, the construction industry’s focus will be on the separation of workers, and enhanced equipment and cleanliness protocols. Separation is a particularly difficult thing to achieve on site, where close cooperation and teamwork are the norm. Therefore, it is likely that smaller teams will be used, with the potential for staggered shifts to limit numbers. With the likelihood that social distancing will continue to be a fixture in 2021 with those working on site required to wear masks, use sanitizer, and keep their distance where possible.
Make way for modular construction
Modern Methods of Construction (MMC) are increasingly being used in the construction industry. Certainly, we’ve seen an uptick in usage, particularly on the part of social housing providers. This no-doubt reflects the fact that recently, processes and materials have become more refined, and industry confidence in MMC is growing. In 2021, it is likely that there will be a huge boost in interest. In the post-pandemic era, both the manufacturing process itself and the results of modular construction are perfectly suited to the times.
Buildings constructed off-site are already built in a way that promotes low worker density. The manufacturing is often undertaken in big, airy buildings, with plenty of room for distancing. The equipment used is also specifically designed to let fewer workers move larger components, reducing proximity, as well as labour costs.
Once constructed, modular buildings lend themselves to growing and evolving businesses, for example, if a company needs individual offices with independent systems, a remote worker requires an office at home, or a hospital needs additional rooms. Prefabricated buildings have the dual advantage of being affordable and short-term or long term, as required. After all, in times of uncertainty, a temporary, flexible solution is often the best option.
Payment disputes
It’s well known that the construction industry often operates on very low profit margins. When project issues arise, cash-flow problems are inevitable. Since the start of the pandemic, the number of construction companies becoming insolvent has been on the rise and it is expected that this trend is set to continue.
With the main concern for many being getting paid and with construction projects rarely running entirely smoothly, if the issue of non-payment does arise, parties may be forced to either bring or defend a claim for non-payment.
In these cases, employers and main contractors alike need to ensure that the appropriate payment and pay less notices are issued in accordance with the terms of the contract. Failure to do so can lead to ‘smash and grab’ adjudications, where a party claims the whole amount of the payment applied for simply on the basis that no payment / pay less notice was issued.
The reality is that smash and grab adjudications are here to stay. Therefore, the key is that paying parties need to avoid leaving themselves open. By checking that they have the appropriate procedures in place across all projects, they can ensure that payment deadlines are met.
Sustainability innovations
The ‘Absolute Zero’ report, published at the end of last year by researchers from a group of UK-based universities, states that the construction industry uses half of all steel and cement produced globally and is responsible for 30 percent of its carbon emissions. If the UK is to stand a chance of achieving its target to achieve net-zero carbon emissions by 2050, this will need to be addressed by the industry as a whole.
From start-ups turning construction waste into bricks, to businesses engineering wood for optimum carbon storage, the world of sustainable building materials is growing at a rapid pace.
With the continued emphasis on using sustainable materials for the long term, and with clients more than ever requesting sustainability specifications, sustainability innovations are only going to continue to rise in 2021. However, for a sector used to tight operating margins, fiscal incentives may be needed to accelerate change, encouraging contractors to make use of the eco-friendly alternatives that now exist.
If you would like to read more like this, then please click here
Related Articles
More Features
- Ten years of progress on payment, pre-qualification and skills
19 May 25
The industry has made significant progress on late payment, pre-qualification, and competence since the formation
- Pagabo provides clarity on impacts of new NPPS and PPNs
12 Mar 25
The Labour government’s new National Procurement Policy Statement (NPPS) sets out strategic priorities for public
- How is the Procurement Act going to drive social value
24 Feb 25
The regulations laid out within the Procurement Act 2023 will go live today.