Sector - Sustainability
Clarity Around Sustainable Materials Needed
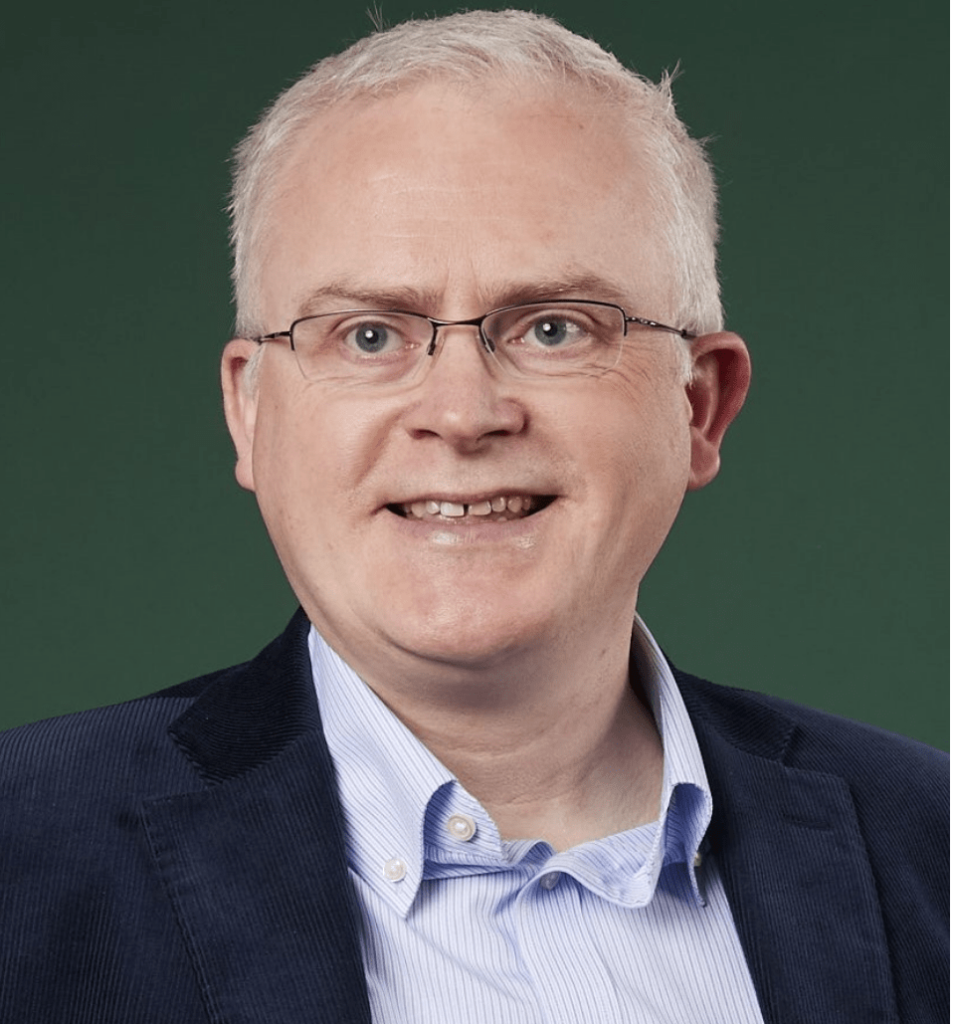
In a bid to reduce the embodied carbon footprint of their structures, particularly large commercial buildings, property developers and specifiers are constantly reviewing the materials they use. However, with little information to go on, it is difficult to make like-for-like comparisons. Simon Cox, head of sustainability at Prologis, the UK’s leading developer and owner of industrial logistics buildings, discusses why clarity is urgently needed to assist the industry in achieving net zero carbon emissions by 2050.
With sustainability climbing the corporate agenda, many businesses are actively looking for ways to reduce their carbon footprint. In the construction sector, the focus has been reducing operational carbon emissions by ensuring that new commercial buildings are well insulated, have plenty of daylight and are fitted with cutting-edge, energy-efficient lighting, heating, and ventilating systems. However, with at least 11 percent of global carbon emissions coming from building and construction materials, tackling levels of ‘embodied carbon’ is just as important as ensuring a new building is energy efficient.
The Government’s recent Energy White Paper has reconfirmed its commitment to achieving net zero carbon emissions by 2050. However, there is no mention of the embodied carbon emissions that are generated by the production, supply, and application of carbon-intensive materials, such as concrete and steel work. Despite the lack of steer from policymakers, an industry-led movement is underway, which is aiming to raise understanding of the importance of reducing and mitigating carbon emissions.
Programmes like BREEAM provide a useful and widely understood set of standards for the environmental performance of new buildings. However, developers aiming to construct net zero properties, realise that they need to do more. In order to move closer to their net zero goal, greater collaboration across the supply chain is needed to share knowledge and experience.
By openly sharing their own experiences of net zero logistics property development, companies such as Prologis aim to encourage other organisations in the construction sector to consider their own long-term sustainability strategies for carbon reduction. Having recently published a white paper on net zero logistics property development, the company is also calling for the industry-wide adoption of the UK Green Building Council’s (UKGBC) Net Zero Carbon Buildings Framework. This framework defines the carbon reduction challenge for the wider construction industry, while setting out a path to net zero that is clear and easy to follow.
By working with specialists with access to detailed knowledge of the carbon content of building materials, specifiers and developers are able to make more environmentally conscious choices. When working closely with the developer and the design team, specifiers have a key part to play in reducing embodied carbon and enhancing the building’s operational efficiency. For example, shallow pitch, large radius curved roofs can help reduce the ridge height of new warehouse buildings, whilst maximising the useable internal volume. With careful design, the embodied carbon of the structure can also be reduced through the use of steel roof cladding, rather than a more typical, and expensive aluminium ‘standing seam’ solution.
Before creating net zero carbon buildings, specifiers first need to understand the boundaries of their assessment and their wider sustainability strategy. While their goal may be to use the latest in certification and scientific metrics to reduce operational and embodied carbon emissions, the end user’s requirements must also be prioritised. From mechanical-handling equipment to electric vehicle (EV) charging infrastructure, every decision will have an effect on the site’s whole-life carbon footprint.
As well as considering the environmental impact of each building material used, specifiers should consider whether it is possible to recycle them after use. It may come as a surprise, but low-cost materials can sometimes be the most sustainable. Equally, those with less embodied carbon may lack longevity and need replacing more frequently. Despite making up over 50% of an industrial building’s carbon footprint, embodied carbon cannot be eliminated altogether. Developers should therefore consider ways to mitigate or offset these emissions. For example, by working with charities such as Cool Earth who are actively protecting the rainforest and supporting the communities that live there.
As the UK moves closer to its net zero by 2050 goal, specifiers have an important role to play in helping to reduce embodied carbon in the built environment, but they can’t do it in isolation. Specifiers, developers and industry bodies must work together to share best practice and support the take up of initiatives such as the UKGBC’s Framework. They should also share what they have learned about sustainable building materials and their supply chains. Greater collaboration will support the evolution of a standardised approach on the way to a more sustainable future
If you would like to read more stories like this, then please click here
Related Articles
More Sustainability Features
- Solar on all new homes must align with 1.5 million homes target
20 Jun 25
The Government have said that solar panels will be included in the FHS, leading to installation on the vast majority of new build homes.
- The renewables revolution in the Scottish Highlands
25 Feb 25
The Highlands are at the heart of a transformative renewables revolution, poised to lead a generational shift in energy production.
- Government correct to head off Climate and Nature Bill
7 Feb 25
The ‘Climate and Nature Private Members’ Bill’, seeks to set new legally binding targets for climate and nature.