Sector - Sustainability
Project to product thinking: The Golden Thread
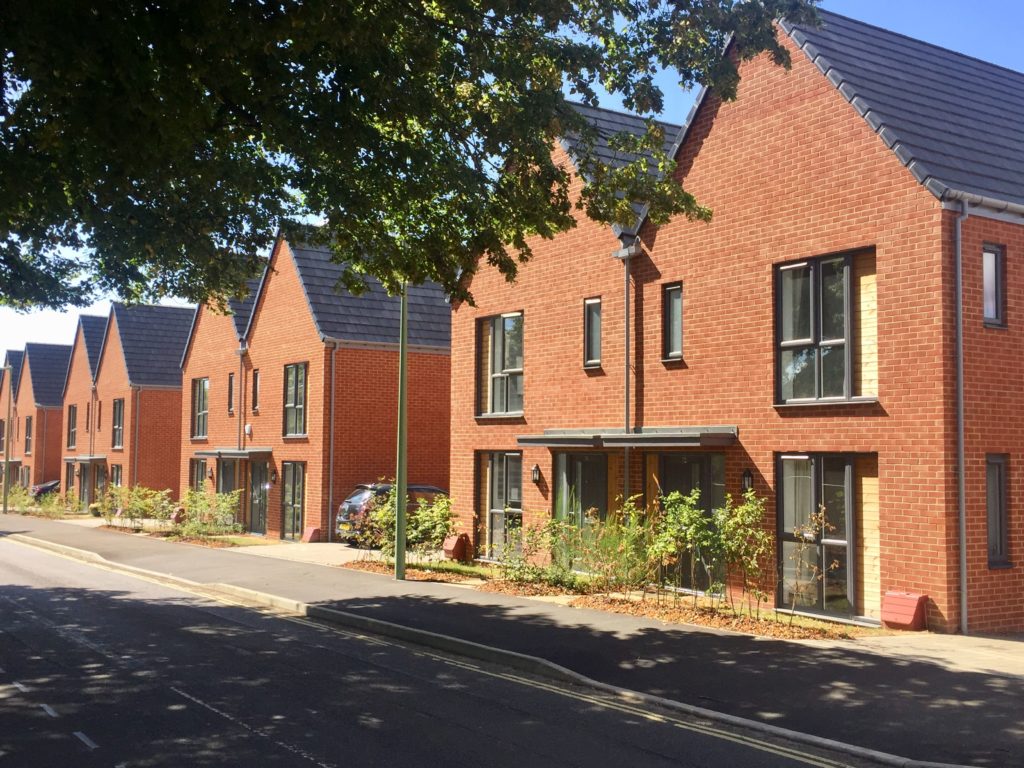
In less than five years from now, I believe offsite will be considered a mainstream method of construction, rather than the secondary alternative which it is seen as by many today, says Robert Clark, Head of Business Development at Fusion Building Systems.
The key to making this happen, he says, lies in how we approach each project and the technologies we choose to use to make it all happen.
The Government has announced a £170M budget for its Transforming Construction programme – an initiative designed to modernise the way we build. One of the objectives of this programme is to help industry make greater use of digital, manufacturing and integrated energy technologies in the delivery of new buildings. At the moment, construction projects are labour-intensive and productivity lags relative to other sectors. But, we have the technology and we can transfer knowledge from other industries to help us improve output, quality and sustainability.
Taking a leaf out of the automotive industry’s book, the Government has stated construction would benefit from moving towards a manufacturing-led approach – viewing output as a product rather than a project. Offsite provides the ideal environment for making this happen.
At Fusion we have been on this page for a while now – and not just because we’ve been working in offsite manufacturing for 20 years. We know the difference technology will make to the construction sector and we know the way the industry approaches production needs to change.
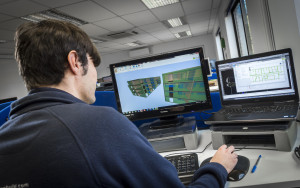
Technology is transforming Fusion’s offsite solution
Anyone who’s heard one of my presentations, either on a visit to our manufacturing facility in Northampton or at an industry event, will know I talk passionately about something we’ve branded internally as ‘JEDU’. This is our abbreviation for moving from proJEct to proDUct thinking: taking the construction industry away from seeing developments as individual silos with unique requirements, limited R&D and rising costs, to adopting a product-led approach, as the manufacturing industry has done for years. This would offer a selection of specific products which can be matched and tailored to development requirements, offering superior levels of quality and scope for innovation.
And, we’re doing more than just talking about it. Two years ago, we recruited a new Operations Manager into our factory. Steve Alder came from the automotive industry and knows what an efficient production line looks like. Over the past 24 months he’s been working with us to streamline our processes and help us educate developers, contractors, architects and supply chain managers about the benefits that a product-led approach to construction can bring. But that’s only half the story – the enabler to make this change in thinking and behaviour happen is technology.
BIM and related emerging digital technologies make up the ‘Golden Thread’ which needs to run through all stages of the supply chain and, importantly, through the people who are controlling the building, commissioning individual partners. To achieve ultimate efficiency, these people need to immerse themselves in the delivery platform which new technologies can provide – procuring the right component parts which are proven, through testing, to work together and will link with the key skeleton technologies in a building. This can only be achieved by adopting a product-led approach, turning the construction model we’ve worked to for decades on its head.
In the UK we’re really still in the early adoption phase of BIM, but give it a few years and we’ll see in the UK what’s happening in Germany now – the tipping point to mass market adoption. Look back 20 years and CAD CAM was just starting to be introduced for offsite design; now, heading into 2019, we operate a design office at Fusion which is fully immersed in BIM and chomping at the bit to take technology further. Last year, for example, we invested in Dalux Field: using this interactive technology, site managers can mark their physical position on a plan, click into a 3D BIM view and provide accurate information there and then about any issues they’ve found. Live reporting can even be streamed into meetings taking place elsewhere between client and contractor, providing an insight into a project for someone who may not have even set foot on site. By working in this way, a fully auditable history can be developed of communication, issue rectification and close out – and because everyone on the team has an immediate visual understanding of what’s happening on site, build delays are reduced and lines of communication are kept crystal clear.
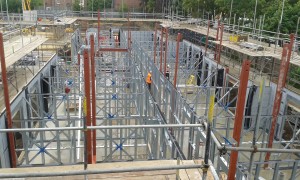
Only three or four skilled erectors will be on site for the assembly of a Fusion light gauge steel frame
Bringing technology into the boardroom in this way also hints at how eagerly there needs to be an acceptance and understanding of its capabilities outside of the design office. It will soon no longer be acceptable for the technophobes among us to compete in this market – we have to upskill our processes and our people if we’re to succeed. My son is of the ‘Minecraft Generation’ and I’ve seen first hand how this computer game is inspiring young people to engage in building design and complex problem-solving. These ‘kids’ are the future of the construction industry but we need to adopt technology now to ensure we modernise, we innovate and we capture their interest to help drive us forward.
At Fusion we invest heavily in apprentices – bright school and college-leavers who can find their way around design software faster than I can fathom my iPhone. Fast-forward 20 years from now and they’ll be in jobs which haven’t even been imagined yet – jobs which will create beautifully designed buildings which are innovative, sustainable and cost-effective, delivered through a production line process. Technology will make this happen, changing the way we work and moving us from a project-led industry to a more efficient, more intelligent product-led sector – offsite.
Related Articles
More Sustainability Features
- Solar on all new homes must align with 1.5 million homes target
20 Jun 25
The Government have said that solar panels will be included in the FHS, leading to installation on the vast majority of new build homes.
- The renewables revolution in the Scottish Highlands
25 Feb 25
The Highlands are at the heart of a transformative renewables revolution, poised to lead a generational shift in energy production.
- Government correct to head off Climate and Nature Bill
7 Feb 25
The ‘Climate and Nature Private Members’ Bill’, seeks to set new legally binding targets for climate and nature.