Sector - Education & Training
Rebuilding UK Construction to Ensure its Future
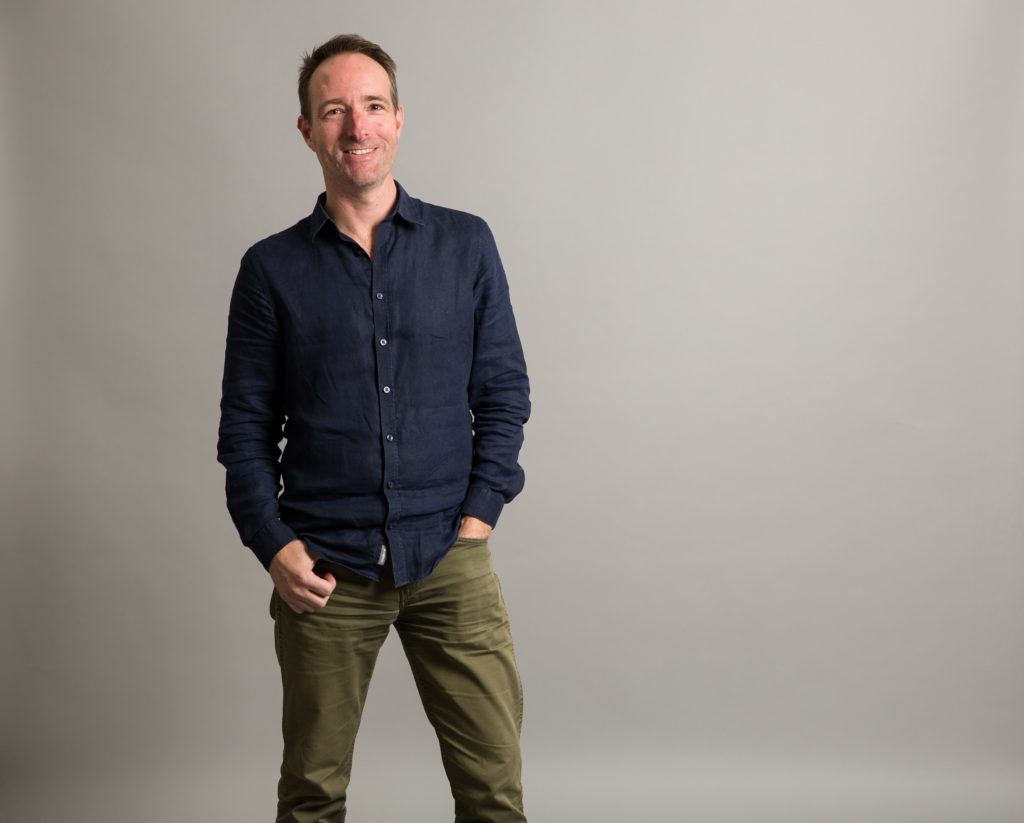
Construction was one of the first industries that returned to work during the Covid-19 pandemic. The key to the sector bouncing back to full strength will be adaptations, not just to PPE and health and safety, but to improved ways of working too. Modern construction technologies can help in the short-term with improved productivity and, in the long term, encourage more young people to the sector to address its skills gap. Here, Gareth Randle, sector specialist at R&D tax credit consultancy ForrestBrown, examines a roadmap to innovation in UK construction.
2020 should be regarded as a watershed moment for the construction industry. From the devastating impact of Covid-19 on a global scale, to the ongoing Brexit saga, and the need to stand up to heightened environmental scrutiny, it’s a real marker in the sand. But these turbulent times are also an opportunity to embrace change and all that comes with to better protect our future.
Time to adapt
Lockdown has swiftly revolutionised how we work; it has exposed the vitally important role that technology plays across all industries – including construction. Whilst the sector was one of the first to get back to work out of necessity, more construction firms than ever before have found new, agile and innovative ways for their workforce to be able to plan, design, build and deliver work.
The challenge is that many companies often don’t feel equipped to take an initial financial risk to invest in the right technology as they are already working to such tight budgets and margins. However, if they can innovate now, they will reap the rewards. Indeed, forward-thinking construction companies who had sagely invested in technology before the pandemic have come off far more financially robust and resilient today than those which are lagging behind by still using outdated construction methods and techniques.
The sector has for a long time felt stagnant, but the landscape is now changing rapidly – and the behemoth is at risk of falling even further behind if it can’t move with the times and harness new technologies. Not only are we facing a long-standing skills shortage, we also need to appreciate that automation and AI is here and will become more prevalent in our daily operations in the future.
Addressing the skills gap
Barriers need to be broken down when it comes to recruiting the right skillset – machine learning and automation will see many repetitive low skill jobs on site replaced with artificial intelligence, whilst existing job roles will have to become more fluid and adaptable. With that in mind, the industry needs to recruit from a broader talent pool which includes coders and tech savvy problem solvers, rather than being so reliant on the more traditional workforce if it is to survive and thrive. That means repositioning the sector as a desirable career to attract the right talent by highlighting the changing face of the industry.
That’s not to say that traditional techniques will disappear completely. The industry looks likely to split into two areas – boutique services for more traditional and artisan skills, and mega projects where repetitive designs and processes take place.
New kids on the block
When it comes to mega projects, new players are swiftly moving in, with cutting-edge digital companies such as IBM and Google already rapidly diversifying and moving into the sector, shaking up slower, traditional building methods and techniques. As they swiftly innovate to streamline processes, save time and money, and increase productivity, these companies will rewrite the history books by showing very different ways of working in construction. One thing is certain – consultants working on IBM-partnered and Google-driven builds who come out on the other side of the process will have some incredible insights at the end of it.
The pace at which tech companies are moving into the sector with a raft of innovative solutions is mind-blowing, but it is those construction businesses who can see opportunity to leverage these exciting developments who will truly stay ahead of the game. Examples include using GPS-based apps and wearables to help with social distancing and safety on site, exoskeleton vests to aid with health and safety, drone surveys, IOT sensors giving real-time feedback on building and material performance, robots that can operate in small, confined or dangerous spaces, plastic roads, modular builds, reuse of materials, digital twinning and beyond.
Time to unite
A further issue is trust. For a long time, many construction firms have been setting themselves up for a fall by not sharing experiences and knowledge with one another when those perceived competitive barriers are out of touch. What’s more, there is little cohesion or consistency when it comes to selecting a unified method of working across the various disciplines in the sector. For example, some companies may be fully BIM-integrated, whilst some may still be using incompatible file formats or even freehand drawing. The system is fragmented and needs to change – we need to find a common format using just one common language that people can adopt, and find ways to either incentivise or drive down the costs of adoption.
Construction companies need to up the stakes; they need to invest and innovate themselves to survive – and fast. So what’s the opportunity? The industry could certainly learn a lot from the massive leap that was made in the early days of BIM which enabled greater collaboration and sharing, and this approach could be replicated across the whole construction sector.
Unlocking potential
For me, data is the missing link. The construction industry is made up of countless tiny and inconsistent fragmented pieces of information. Construction firms must learn to harness its potential, not least given that some stats[i] point to under 0.5% of data being captured and actually used in construction. This is a wasted opportunity and has to radically change. Data has to be captured, used and incorporated to ensure shared learnings through open source platforms so that everyone in the supply chain can tap into this and evolve together. Similarly, data security and control will also have to evolve concurrently to ensure that this information is protected and cannot be misused.
There are so many exciting opportunities for this sector if only construction firms were prepared to take an initial risk and challenge the way things have gone before. The Government’s Research and Development (R&D) tax credit scheme could hold the key for those SMEs looking to future-proof themselves in the marketplace. It allows companies to venture into the unknown if they have a particular goal in mind, so if a business is taking a risk by attempting to ‘resolve scientific or technological uncertainties’, then it may well be carrying out a qualifying activity, which makes embracing the spirit of innovation more palpable. If human error is removed or one can do something faster or better, then there could be R&D in it.
Where there has been perhaps a reluctance to invest in technology, barriers are gradually falling away, but it has a long way to go. There is no longer an excuse for construction firms not to adapt, and really harnessing technology goes way beyond using ‘low tech’ on site such as Dropbox on iPads or scattershot WhatsApp groups.
Ultimately construction leaders and site managers need to be pushing technology to its limits to accelerate necessary change, reduce human error, minimise waste, drive efficiencies and avoid costly mistakes. Pandora’s box is open and there’s no going back, so now’s the time to take a risk and innovate to drive forward.
[i] Hill, Brian L. “Digging for the Big Data Gold in Today’s Construction Projects.” Xpera Group. 2017.
If you would like to read more like this, then please click here
Related Articles
More Education & Training Features
- Immigration policy must serve Britain, not party politics – NFB
29 May 25
The Government has published a new White Paper which sets out major reforms to the UK’s immigration system.
- Moving beyond EDI to embed good employment
11 Apr 25
The benefits of EDI - higher retention, more productive teams, and healthy morale - are crucial.
- Universities fear government reforms will stifle construction sector demand for higher and degree apprenticeships
3 Apr 25
Industry fears forthcoming apprenticeship reforms will deter many construction firms from upskilling their workforce.