Features - Business
Time to modernise – Exclusive interview with Mark Farmer
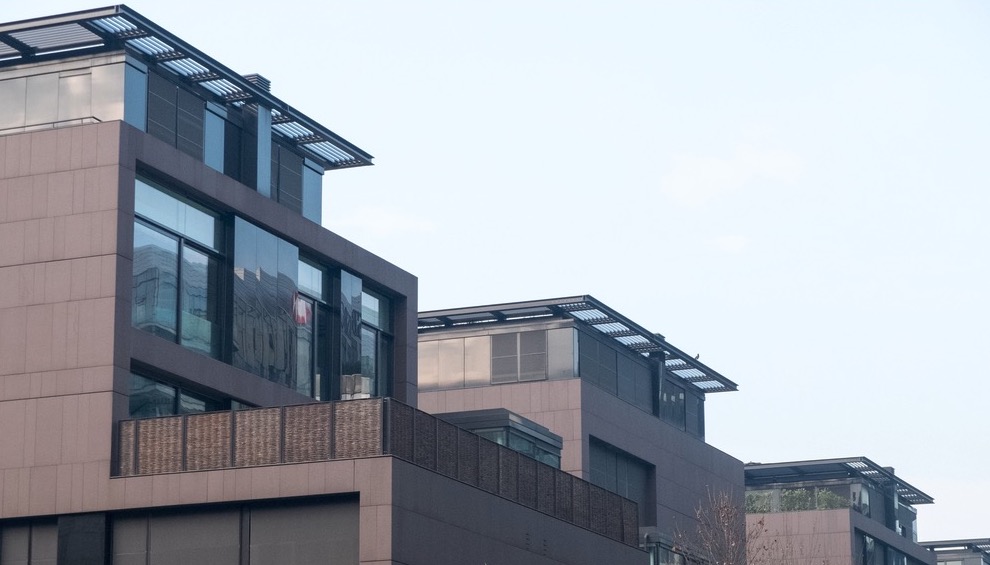
UK Construction Online’s Matt Brown speaks with Cast CEO, Mark Farmer, about how offsite manufacturing can modernise the construction industry, improve building standards and help solve the skills crisis.
Mark was commissioned by the Construction Leadership Council, at the request of the ministers for Housing & Planning & Skills, to undertake an independent review of the UK’s construction labour model. It looked in particular at the skills pressures and other constraints that limit housebuilding and infrastructure development in the UK.
The result was Modernise or die: The Farmer Review of the UK construction labour model, which called for radical steps to be taken to address the sector’s longstanding problems.
The title of your report was ‘Modernise or Die’ but what are the real consequences if the industry fails to take the opportunity to modernise?
We are at a crossroads in terms of the both the risk and opportunity to the construction industry. I think we have some unprecedented pressure points that we haven’t seen in the industry before.
There are two very specific issues I would highlight that mean the timing of my report is perhaps more critical than in other instances where high profile industry reports have been launched.
Firstly, the demographics of our industry are such that we are now consistently losing more people every year than we are gaining. As people retire, we are not bringing through enough homegrown talent into the industry. That’s true across not just the onsite construction trades but also in the professions such as surveying, engineering and architecture. It is quite an insidious problem that is creeping up on us but it’s gathering pace.
Secondly, we have the potential impact of Brexit. This is an unprecedented event that could disproportionately affect construction from the perspective of the industry’s high reliance on migrant workers, particularly in London but actually it is also a broader issue across other regional towns and cities in the UK.
What plays out over the next few weeks, months and even years could have quite radical implications on the resourcing profile available to the construction industry.
If you combine the Brexit risk with the issue of the ageing workforce, plus the fact that we are still struggling generally to attract youngsters into our industry, then we have a unique combination of pressures that mean we have to do something differently, it is no longer a choice, as perhaps it was when the Latham and Egan Reports were launched in the 1990’s.
To my mind, we haven’t seen this level of risk before and with technology and the advent of new ways in which we can deliver, we now have a fantastic opportunity to grasp that chance to do things differently in the face of such significant challenges.
Do you feel the government need to do more to encourage new methods of construction to meet the shortfall in housing?
The Housing White paper was definitely a step in the right direction. The content and issues that were identified are the right ones. There is a recognition these issues can’t be solved overnight but what the Government committed to do is recognising it has a role to play in pump priming demand for the pre-manufacturing and offsite market, which was recently ratified by the CLG Select Committee.
To build capacity in that market, which is currently quite fragmented and immature, we need that sector to grow and to grow sustainability in response to increased client demand. While industry comes to terms with the fact that it has to change the way it delivers, the Government can take a leadership position and actually start commissioning work using pre-manufactured techniques.
The HCA’s Accelerated Construction Programme, which is a very specific initiative that the government has set out, combined with the Home Building Fund, will provide £5Bn of combined funding and is quite clearly established to do that very thing.
From my perspective, the Government understand the potential but it is about pace and scale.
What we need is real commitment is terms of putting significant sums behind different ways of delivering that enable the industry to have confidence in the levels of investment needed to establish more offsite manufacturing capacity.
What would you say are the biggest obstacles to the industry embracing offsite construction?
There is an ingrained culture in the construction industry, which is just against change. It’s hard to put your finger on, but some of it is that people have grown up, trained and worked in an industry which has always done things a certain way.
There is quite a deep-seated reluctance to change the way that we deliver and that is something that isn’t going to go away easily. It’s going to take time to overcome suspicions, scepticism and the lethargy around realising as I have already made clear, that we simply have to do things differently.
I think the challenges around Brexit and an ageing workforce will force the issue. So even those that don’t really believe they should be embracing modernisation, will face a time when they have no choice and will be influenced by peer pressure as the market starts to marginalise business as usual.
There is a dawning recognition that’s sweeping the industry at the moment that there are some significant problems ahead and people need to get ready for what that means around their own role, their business’s health and market positioning..
These issues need to be addressed now, not when it’s too late and when all of these problems are right upon us.
Another barrier is the very tangible issue of the level of investment some of these techniques involve. For people who want to consider establishing new factories or offsite techniques, there are considerable amounts of money involved in doing so.
Unless there’s clear line of sight to where the demand is, then it could be a high-risk decision, which comes back to my point about the Government having a key role to play in proving there is a minimum level of demand for these new techniques.
Also, some of the issues relate to the perception of pre-manufactured or what has historically been termed ‘pre-fab’. In the housing market there is still a perception of what ‘pre-fab’ represents linked to poor quality, temporary type housing rather than what it can be now – truly permanent, 21st century precision engineered manufactured components. The recent quality problems experienced in traditional delivery also call into question the long held beliefs that artisan trades can deliver a better solution.
We need to go on a journey that not only educates the industry but also the wider public and funders. The Government also has a key role in an accreditation and warranty system that might sit behind this emerging new sector.
Do you think there is a concern from traditional construction workers that these new methods could put them out of work rather than an opportunity to retrain?
Yes, there is definitely a sense that this would be seen as a threat. I can understand that; it is only human nature.
Workers may have concerns that their skills are no longer relevant leaving them redundant in some shape or form. Even though that is an understandable reaction the reality is we need to educate everyone as to what the opportunities are in skilled craftsmanship alongside retraining to new skills in digital and manufacturing led careers.
The first point I would make is that we will never in our industry be delivering more than just a proportion of what we do using pre-manufactured techniques. We will always have a significant component of what we do being built traditionally.
It still needs to be built better traditionally in terms of the efficiency of the process that we use and in some cases the quality that is achieved, but we still need traditional trades like bricklaying and carpentry and a large amount will always be site-based. That’s the nature of how we deliver – we can only do so much in a factory.
The bigger thing for me, as referenced above, is making people aware of the re-training and re-skilling opportunities that could make their working day and career much more interesting.
The ability to not only be involved in site-based traditional working but to combine that interfacing with factory-based products -how you might be engaged in hybrid working and embrace robotics and automation on construction sites.
There is an opportunity for tradesmen to become quality control supervising technicians rather than someone who is physically laying a brick or cutting timber. There are some really interesting career opportunities if people take a step back and receive the right kind of guidance and leadership.
It’s difficult for people on the ground to understand what this might mean for their own welfare. It requires leadership and people to explain what it could look like for individuals concerned and that this is not a threat to their livelihood.
Could offering a more factory-based working environment make a career in construction a more attractive proposition?
You have to look at the issue from two angles. Firstly, from the existing workforce’s perspective you have the re-skilling opportunity already described or a refinement of what they do and continue to do so alongside new techniques.
Secondly, you need to look at the possible impact on attracting new entrants. As we discussed earlier, one of the biggest issues we have, against a backdrop of Brexit and an ageing workforce, is that we aren’t attracting enough youngsters into our industry.
When people visualise being involved on a construction site, they immediately see being out in all kinds of weather, physical exertion, higher health and safety risks and these points, whether perception or reality, don’t help make our industry a priority choice for kids.
If you retain the element of a site-based involvement, I think that actually adds to the uniqueness of construction, and not being stuck in a constant office or factory environment will be seen as a positive for some kids.
But if you can then bring that experience alongside factory-based manufacture-led processes with a controlled indoor environment using digital technology, then there is a massive opportunity to step change the attraction of the construction industry for young people coming in.
That exciting future construction skills landscape can be conveyed in schools to kids as young as ten years old, if not younger, to give a revised narrative about what construction actually represents, rather than dive in and talk straight away about the way we have always done it with architects, surveyors, engineers, contractors and sub-contractors and showing images of building sites with projects being delivered in the traditional way.
There is a real opportunity to completely redefine what the contraction process looks like and bring a lot of it more closer to the manufacturing sectors and then bolting on the end the fact we haves site-based assembly and construction.
Is there enough collaboration between industry, educators and government to ensure offsite construction can be maximized?
The simple answer to that is no. Our industry is not known for collaboration and sharing concepts and ideas. It’s not known for wanting to embrace the idea of working with others for the greater common good. I think that is something definitely that as a structural issue the industry needs to overcome.
Again, a lot of it is driven by culture. People have been trained and brought up in the industry in a certain way – it’s adversarial, it’s very contractual and is about people protecting positions on different sides of the contract. We need to overcome that with recognition that we need more collaborative shared and aligned interests.
I’m a bit of a sceptic when it comes to just promoting or preaching about collaboration in isolation from a real means of embedding it into industry. I do not believe from my experiences of being in the industry a long time that by just saying we should all be collaborating – anything is ever going to happen. The industry doesn’t react to that kind of stimulus, what it will react to though is disruption and competitive threats.
By changing the delivery to a more of a pre-manufactured model utilising offsite technologies, combined with onsite process improvement changes, the physical way in which parties have to work together will force the issue of collaboration.
Some people will get it and treat it as an opportunity. Others won’t be able to change their behaviours. That is a very clear dividing line between those that are going to be successful going forward and those stuck in the past.
It would be nice to think that rather than pushing people on the journey to work collaboratively that you could attract people to doing so because it is a good thing to do but unfortunately in our industry its going to require a push I’m afraid.
It will be driven by some of the pressures we now have on resource shortages and manpower. That’s going to drive the agenda whether we like it or not.
Do you think that the BIM mandate can act as a catalyst to the adoption of offsite construction and collaborative working practices?
I understand why the Level 2 BIM government mandate was introduced but I’m not a believer in mandating digital technologies in isolation from influencing the physical delivery models that we use.
My view is, again, similar to collaboration, if you just say this a good thing to do people will not listen in our industry. On public sector projects where you are forced to do it, then the industry will, to an extent, play the game and do what it needs to do but it won’t really embrace the potential of digital engineering.
You have to reverse the issue and if there is any mandating to be done, it should be around the physical model of how we deliver using design for manufacture and assembly led pre-manufacturing because that will force the issue around the fact that most of that approach would only really maximise efficiency if it uses digital platforms such as BIM.
So rather than leading on BIM or collaboration in isolation, my view is you have to concentrate on the hard, physical way we deliver construction and the other two things will come with it as a natural consequence.
BIM can be a massive enabler. It enables us to deliver digital design, manufacture and assembly in a completely different way to traditional construction. The collaboration is then forced because the actual integration model is very different and you don’t have that hierarchical split between clients and their design team and the supply chain – its fully integrated and more in line with a manufacturing model.
Do you believe that modern methods of production can help improve standards as well as deliver greater efficiencies?
There is a great opportunity to address what is a growing concern about traditional construction quality, particularly in the housebuilding sector.
We have a seen an increase in media interest in poor delivery quality in the housebuilding sector over the past six months. I believe there are a lot more stories to come that you will find pretty shocking about how traditional construction, poor workmanship, design and supervision have contributed to a sub-standard product that wouldn’t be acceptable in any other industry.
The clear challenge and opportunity for offsite and pre-manufacturing is that if you are going to use fully precision engineered, digitally enabled techniques of assembling products, ensuring ultra tight tolerances, interface working, that can absolutely overcome all the issues and risks you have with onsite materials and workmanship assembly.
The biggest risk is that the emerging offsite sector replicates some of the problems that the traditional industry is experiencing. If we had a situation where too much demand was placed on too small a supply of capacity in the offsite sector, it is likely mistakes would be made. That is the big risk constraining what is a potential opportunity.
There’s also big difference in some of the solutions out there in the offsite sector. Some of them are fully digitally enabled, high tech and underpin quality; others aren’t that dissimilar from traditional working but just done in a factory environment.
Absolutely, the offsite sector has an opportunity to embrace high quality and be seen as a byword for better quality than traditional but it also needs to learn from the problems traditional industry has had and grow sustainably with the Government’s help.
If you would like to read more articles like this then please click here
Related Articles
More Features
- Ten years of progress on payment, pre-qualification and skills
19 May 25
The industry has made significant progress on late payment, pre-qualification, and competence since the formation
- Pagabo provides clarity on impacts of new NPPS and PPNs
12 Mar 25
The Labour government’s new National Procurement Policy Statement (NPPS) sets out strategic priorities for public
- How is the Procurement Act going to drive social value
24 Feb 25
The regulations laid out within the Procurement Act 2023 will go live today.