Features - Design
When modular met medical: healthcare facilities get a dose of efficiency and quality
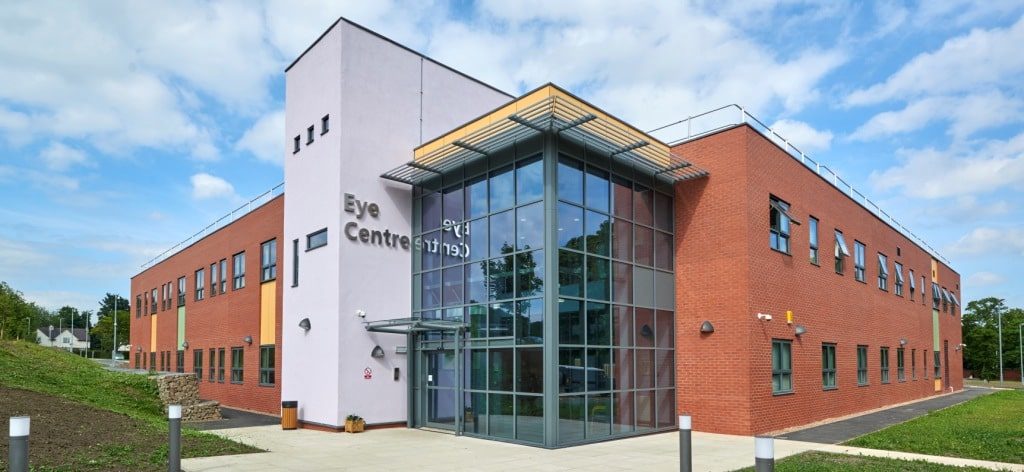
There has been much talk of late about recent studies revealing that while most industries have seen impressive increases in efficiency and productivity in the last few years, the architecture-engineering-construction (AEC) industry has somewhat lagged behind.
Experts agree that this is mainly due to architects, contractors and subcontractors working in silos. They also agree that the healthcare sector has suffered most from this lack of progress due to the complexity of medical facility buildings and their very specific requirements, such as NHS compliance. Modular buildings are fabricated under controlled plant conditions, using the same robust materials as more traditional construction projects. This, combined with the rigorous adherence to building codes and standards makes offsite construction as, if not more, safe as conventionally-built facilities.
Improving collaboration to lower costs
By definition, modular building requires close collaboration between architects, contractors and subcontractors early in the building process. By eliminating silos and fostering a greater sense of teamwork, the modular building process results in better upstream decision-making, which helps keep projects on time and on budget.
Off-site construction is also protected from various sources of costly delays. Weather-related risks are minimised, and labourers are able to operate in safer working conditions – in a controlled environment, rather than facing the elements in a less contained working environment.
The offsite construction process provides opportunities to cut costs by increasing the efficiency of the materials purchasing process. By keeping construction in a protected manufacturing environment, the risk of damage or theft of equipment and materials is also greatly reduced.
Cutting construction timelines
One of the most valuable advantages to offsite construction for the healthcare sector, however, is a reduced time to occupancy. With a modular construction project, the offsite building process can take place in parallel with on-site preparation; project timelines are thus halved.[1]
It goes without saying that minimising the impact of construction on existing parts of a hospital or medical centre, where vulnerable patients may be undergoing delicate procedures, or simply trying to rest and heal, is also a top priority. Plus, since the very nature of medical facilities usually places them in built-up areas, where access is easy access for staff and patients, managing disruption to surrounding homes and businesses is another major concern. Off-site construction overcomes these challenges whilst offering a host of performance benefits – from increased scope for customisation to the latest innovations for greater sustainability, and of course Considerate Construction also at the forefront.
The anatomy of an offsite healthcare facility
In June 2015, Pinderfields Hospital in Wakefield chose a two-storey modular solution for their new Clinical Support Unit for Ophthalmology. This permanent building, created to house an advanced eye clinic and state-of-the-art office space, was constructed using the latest Ibex steel-frame modular building system which allowed large elements to be completed off site.
With a facade clad in a combination of facing brick, render, and Trespa® panels, the building benefits from the latest ducted air conditioning technology for managing internal environments within clinical areas. Ecological features incorporated into the design include increased levels of insulation, low-energy lighting, energy-efficient heating systems, and water-saving technology.
Not only did this building achieve BREEAM Excellent rating, it was completed in just 32 weeks -including site remediation and external works.
Modular moves healthcare facilities forward
As more and more decision-makers in the healthcare industry become aware of the benefits of choosing high-quality, cost-efficient, and attractive modular buildings that are quick and safe to construct, the AEC industry is likely to see a boom in projects like the Pinderfields Ophthalmology unit. The prognosis is highly positive for both the healthcare sector and the modular building industry.
Find out more about Elliott, the principal contractor for the Pinderfields Hospital Ophthalmology building.
[1] https://www.thomasnet.com/insights/4-reasons-why-building-professionals-are-switching-to-offsite-modular-construction/
If you would like to read more articles like this then please click here.
Related Articles
More Features
- Why early MEP design collaboration holds the key to smarter buildings
24 Jun 25
Working closely is essential to ensure that all aspects of a building’s design contribute to
- BSI publishes groundbreaking standard for MMC in residential developments
28 May 25
New specification to build confidence in modern methods of construction (MMC) for residential developments has
- Pagabo provides clarity on impacts of new NPPS and PPNs
12 Mar 25
The Labour government’s new National Procurement Policy Statement (NPPS) sets out strategic priorities for public