Features - Business
Energy Supply: How to fight metering delays
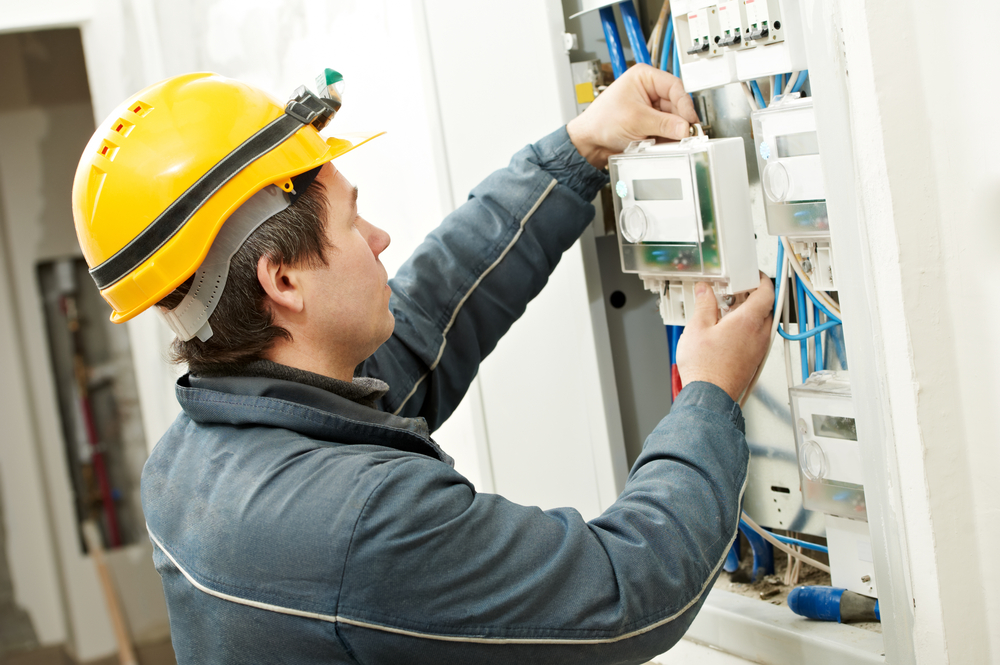
Recent years have seen rapid development of new technology which will inevitably affect the future of construction. The next industrial revolution is about to transform the construction sector as we know it: the robotisation of construction workforces, 3D printing, connected cities and cyber security have already started shaking things up in the industry.
With such technological transformations on everyone’s tongue, it’s easy to overlook some of the smaller but important innovations taking place that impact the construction industry, including the rapid increases in the time it takes to get an electricity meter fitted in – something that site managers have often underestimated.
Many have encountered scenarios like those and at npower Business Solutions (nBS) we hear from our customers on a regular basis: groundwork issues delaying new power supply, then site managers losing track of time and the need to arrange metering and supply on site; even as deadlines to commission and hand over creep ever-closer.
Waste not, want not
There is nothing more frustrating on a large construction project than such instances. Deadlines can crack under pressure and all sorts of unanticipated issues can crop up on a site. When managers belatedly pick up the phone and learn that typically it takes between 15 and 20 days to get a new meter, it can truly be panic stations time.
This can result in delays, unnecessary additional costs – for example in generator hire – and waste. The UK Green Building Council claims that of the 400 million tonnes of materials delivered to construction sites each year, around 15% end up in landfill as a result of inefficient ordering or storing; including, no doubt, site managers failing to recognise the impact power delays has on project deadlines.
It doesn’t have to be this way. And for those who know where to turn, it no longer is.
Faster power, faster projects
Recent partnerships have allowed the time it takes to secure customers a live new meter to be cut by 75% over the past year, bringing it down to just five days. To make the most of this though, site managers – or whoever is responsible for ensuring a meter is in place on time – need to be aware of a few things; not least what goes on behind the scenes after you pick up the phone to a supplier.
Firstly, the request has to go through a registration process, with the supplier notifying the national database. It can take several days to gain acknowledgement and registration. After this is accepted, the supplier has to appoint a meter operator, a data collector and a data aggregator. Each of these three parties has to accept the appointment. (It usually takes three working days to get each of these acceptances back).
Only when all the acceptances are in hand do suppliers request a metering date in the diary. Once this is done, a dataflow is sent out with a 10-day working notice period.
That’s the long-established process.
Shaking things up
However, this status quo has now been challenged.
For example, nBS is an approved meter operator as well as an energy supplier, which means it is able to carry out the majority of its metering work direct. And where it can’t, the company has a very close working relationship with its third-party contractor, giving it reliable national coverage for all types of meter installations.
To further support its fast-track service, it has developed an effective in-house system to ensure absolute efficiency when it comes to setting up new electricity supplies and installing meters. Everyone who picks up the phone seeking a new connection, for example, is allocated a dedicated single contact who manages the new connection process from start to finish – and is on hand to help resolve any queries throughout.
Making it work, however, means making sure site managers are quick to get an MPAN (that’s your meter’s unique reference number) over to a potential supplier as soon as the distribution network operator (DNO) – who’s actually dug up the road and put a line in for you – have released it.
The new fast-track service can make the difference between a delayed project and successful completion, particularly on sites where something has gone wrong and there are time constraints. Getting information to the supplier like the MPAN as early as possible remains crucial though. The supplier can then discuss with the DNO whether the site is ready, or when it is due to be, so metering can be aligned.
If you would like to read more articles like this then please click here.
Related Articles
More Features
- Ten years of progress on payment, pre-qualification and skills
19 May 25
The industry has made significant progress on late payment, pre-qualification, and competence since the formation
- Pagabo provides clarity on impacts of new NPPS and PPNs
12 Mar 25
The Labour government’s new National Procurement Policy Statement (NPPS) sets out strategic priorities for public
- How is the Procurement Act going to drive social value
24 Feb 25
The regulations laid out within the Procurement Act 2023 will go live today.